August 22, 2024
Investing in the right construction estimation software can revolutionise your workflow, saving you valuable time and money. The days of painstakingly calculating project costs with spreadsheets are quickly becoming a thing of the past, and you don’t need to be a technical maestro to get to grips with newer alternatives.
We’ve compiled a list of the five best construction estimation software options for UK contractors. These tools are designed to enhance accuracy, improve workflow, and help you win more bids.
Read on to discover the top estimation software that can transform how you manage your construction projects.
4 Types of Construction Estimation Options
Before we get into the nuts and bolts of the best construction estimation software, let’s take a quick look at the four different types out there.
- Estimating Software – Specifically suited for pricing, these tools help contractors save prices and generate detailed cost estimates. Examples include BuildPartner, Price Builder, and Buildxact.
- Project Management Software – While primarily focused on wider project management, such as lead management and site management, these tools often have some basic quote creation functionality. Examples include Houzz and Procore.
- Estimating Services – Professional estimation assistance by experts who provide cost estimates as a service. Examples include Build Aviator, Estimators Online, and My Build Estimate.
- Takeoff Software – Software specialising in listing all the quantities needed for a construction project (but doesn’t feature prices). Examples include Bluebeam and PlanSwift.
In this article, we’ll exclusively cover estimation software, which allows you to generate estimates and quotes for the various stages of a project.
1. BuildPartner
BuildPartner is an intuitive estimation platform that allows you to generate accurate benchmark costs for a project in minutes. It does this by enabling users to share information with each other and creating a live database of thousands of projects, tasks, and materials.
Simply enter the region, select the specification, project type, and construction project rooms and shells, and the pricing tool will populate the estimate and show you average prices in your area. You can then refine specifications, labour and materials rates and margins to suit you.
You’ll have a localised, accurate quote for your build in just a few clicks.
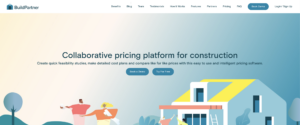
Pros
The wide range of template tasks and projects makes it easy for users of any experience to create accurate quotes and cost plans within minutes.
This speed of cost plan creation is unique and provides a reliable indicator of project cost early in the design process, which is of huge benefit to both contractors and clients.
To create or receive a quote for a project, you simply click your way through a series of five screens—choosing the build type and which rooms are included.
The speed at which you can produce an accurate quotation is unmatched, so contractors can be more agile in responding to requests and tenders.
Being able to produce itemised quotations so quickly is hugely attractive to clients, and many BuildPartner users see a marked improvement in their bid-hit ratio. So, users stand to win more work by producing detailed, accurate quotes.
In the event that a client awards the contract to another firm, you haven’t wasted several hours calculating a quote and researching prices.
BuildPartner is user-friendly and incredibly easy to navigate. It doesn’t have the complex analytical matrix-style dashboard that accompanies other pricing tools. You’ve got everything you need, from project timelines to itemised cost schedules, cost breakdowns, and Excel exports.
Once you’ve created your initial quote, you can refine it by adding and removing any items as required and by overriding room dimensions.
It's one of the few platforms that’s accessible to everyone, from technical pricing teams in corporations to sole traders who are less savvy with IT.
BuildPartner is cloud-based, so it requires no download and can be accessed anywhere on any device.
Cons
Anything is possible with this product; you can edit projects and tasks in minute detail. However, because it is structured, the tradeoff for speed and simplicity is that it’s harder to customise, for example, to create unique tasks and structures for unusual projects.
However, in instances where a particular building material or task is absent, the BuildPartner team is known for supporting users and advising on a reasonable provisional sum to include. The level of service and speed of answering questions is excellent.
Some larger companies may find the limitations on the number of projects restrictive. With BuildPartner, you can quote for the following number of projects for each tier per month: Basic (5), Standard (10), and Pro (15). But they have enterprise options for people going over that number.
Verdict
BuildPartner is an excellent way of quickly providing your clients with quick and accurate estimates. The detailed breakdown ensures your clients have total transparency and confidence in the quoted figures.
An additional benefit is that the subscription doesn't charge per user. Each service plan allows you to invite an additional user, so you won’t be charged exorbitant fees if you’re using within a small practise.
There’s no obligation to pay annually, and you can cancel anytime. It’s also one of the better value options compared to those in this review, by a considerable margin, being over three times cheaper than Buildxact.
Summary
- Cost:
- Starter: £24 + VAT/month
- Standard: £46 + VAT/month
- Pro: £68 + VAT/month
2. Price Builder
Price Builder is a tool that enables the fast and precise generation of professional quotations for clients. It simplifies the pricing process, saving time and reducing errors. Prices are calculated using accurate preprogrammed algorithms.
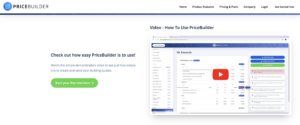
Pros
Price Builder is more suited to those who prefer a hands-on approach to quote generation. Whereas BuildPartner does all the heavy lifting and calculation for you, Price Builder requires you to manually enter the details of projects.
Among the estimation tools reviewed, Price Builder offers the most intuitive user experience. The interface is highly responsive to the user’s actions, with on-page elements popping out, enlarging, or changing colour when hovering over.
If Price Builder was an operating system, it would be more akin to iOS than Android. It doesn’t have that clunky or outdated feel like esti-mate or HBXL.
Aside from being a fluid system, the real benefit of this is the ease and efficiency of quote creation, and you can do all this on the go from your mobile, tablet, or laptop.
The pricing is simple and cost-effective. As with BuildPartner, you can cancel anytime and aren’t trapped in an annual subscription, like HBXL—which features later in this review and costs over £649 per year for its cheapest subscription.
Cons
The biggest drawback of Price Builder is the need to laboriously enter several fields of data manually. This is in contrast to BuildPartner, in which a benchmark quote can be generated in a matter of minutes, in literally just a few clicks.
For instance, when using Price Builder, you start with a blank list of around 20 categories, including Preliminary Costs, Scaffolding, Demolition, Foundations, Walls, and Pitched Roof.
Users then need to enter specifics in each category, such as the quantities and lengths of materials required. You could spend a considerable amount of time quoting for a project for which you may not be awarded, which somewhat defeats the object.
For instance, in the Preliminary Costs category, you’ll be prompted to manually enter information such as Site Supervision (Days), General Builder (Days), Labourer (Days), Drive/Garden/Patio Protection (m2), General Rubbish Skips, and more.
Theoretically, much of this could be done in a spreadsheet since the process is reliant on data entry.
You’ll need to work through every section in order to generate a quote.
Verdict
There’s a considerable lack of reviews out there for Price Builder. As of July 2024, there are no reviews yet on Trustpilot or Capterra, so it’s a company with little to no online reputation.
It’s a fairly time-consuming platform and less suited to those looking to generate quotes at speed. But it’s a decent tool for those who need some organisation and structure when it comes to streamlining their quoting process.
Summary
- Cost:
- Basic: £25/month
- Professional: £35/month
- Pro: £45/month
3. Buildxact
Buildxact is a comprehensive construction management software for estimating, job management, and project tracking. Given that it’s a comprehensive offering that comes with a tonne of other features like lead management, cost tracking, and invoicing, it’s more expensive than the likes of BuildPartner and Price Builder.
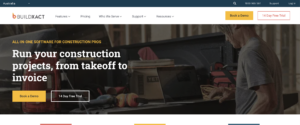
Pros
Buildxact pitches itself as a sophisticated software solution and goes beyond mere estimation. It has a host of other features, such as lead management, customer communication, takeoffs, scheduling, cost tracking, site management, and invoicing.
It’s a one-stop shop for managing construction projects, but it’s not for everyone.
The learning curve is steeper than other software in this review, but once you’ve created your own template for a project, each successive estimation becomes invariably easier.
This is particularly useful if you offer bespoke services and use similar materials and contractors from one project to the next.
To get started, you can create your estimate using one of the five default templates: Duplex (Single Storey), Extension, Kitchen and Bathroom, Landscaping, Single-Storey House.
However, this is a fairly limited offering compared to the plethora of selections available when using BuildPartner, which covers all manner of build types (refurb, remodel, extension, builds) and a variety of rooms and shells.
After generating a quote with Buildxact, you’ll be presented with a professionally formatted document, which features a slick Gantt chart schedule that is likely to be appreciated by project managers, who always want to know what is happening and when.
The other huge time-saver is the ability to integrate the software with supplier catalogues and accounting software such as Xero, Quickbooks, and Deputy. It’s the only software in this review that allows for integrations of any kind.
Cons
Estimating a project’s cost with Buildxact is a slow process, even when a decent template is used. It requires a lot of line-by-line reviewing and checking to ensure everything is captured.
There are over 40 categories for which to enter data, and you need to upload plans, which may not always be immediately available when a client requires an indicative quote.
This exhaustive list comprising over 40 categories, when viewed together, requires an excessive amount of scrolling. Navigation with Buildxact represents a challenge, even when zooming out in the desktop version.
Those looking exclusively for estimation service rather than a CRM system would be better off starting out with a more convenient solution like BuildPartner—one which has a steady learning curve.
When using Buildxact, the chatbot pop-up notifications are particularly invasive and get in the way. It’s only a small peeve, but it’s a distraction nonetheless.
Despite being a cloud-based software solution, Buildxact only recently released an onsite mobile app. It has limited functionality and can only be used to manage and view updates rather than generate quotes. What good is the app if it cannot perform its primary function?
Also, the free trial only lasts 14 days, which doesn’t feel long enough to fully explore the system.
Verdict
Those looking for a complete CRM solution that includes estimation software may find Buildxact to be a cost-effective solution, but it comes with a steep learning curve.
Users should be aware that plans must be uploaded and data entered manually to generate an accurate quote. It’s not a mobile-friendly software solution, which makes it difficult to access and amend quotations when on the go.
Summary
- Cost:
- Entry: £88/month (billed annually)
- Pro: £160/month (billed annually)
4. HBXL - EstimatorXpress
Whether your converting a loft or undertaking a new build, HBXL’s EstimatorXpress can be used for projects both large and small. HBXL also offers other complementary project software, such as PlansXpress, BuildProjex, Health & Safety Xpert, ProjectXpert, and ContractsXpert.
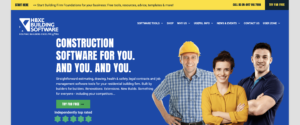
Pros
HBXL offers hundreds of estimating templates to get you started, from renovation work to extensions, loft conversions to new builds.
Each template is made up of the relevant estimating calculators (over 600 in total) to get you quoting quickly. Take, for instance, the ‘attic block wall’ calculator. It’s loaded with priced blocks, steel to build the wall on, plaster, skirting, materials for decoration, and the associated labour.
Simply scroll down the categories and answer a few questions in each. Most of these questions appear in the form of dropdown lists or check boxes, which makes the process much simpler than having to manually key in information like when using Price Builder.
Once you’ve worked through the categories (Floors, Roofs, etc.), simply enter your dimensions and tweak the spec to generate your quote.
Material prices are live, too. The built-in price book, Price Tracker+, keeps your price book up to date by scouring the internet for the latest prices.
And if you have your own special prices or labour rates, you can change them as you see fit. Your quote is fully customisable. The fields are pre-populated for each trade. You can leave it as is or adjust it to reflect your local conditions.
HBXL reports are about the most advanced available in the software options presented in this review. These readymade reports show you cash flow projections, a breakdown of your plant costs, your spend on labour hours, and your sub-contractor outlay, and they allow you to keep track of all your expenditures.
Cons
It’s unusual in this day and age for premium software to come in a downloadable format rather than being cloud-based. When using cloud-based software like BuildPartner, you can access it from any device, anytime—for convenience.
Not only that, but cloud-based platforms receive automatic updates, ensuring users always have the latest features and security patches without having to manually update.
Be aware that EstimatorXpress takes up nearly 1GB of your storage
It’s also a huge inconvenience if you just want to undertake a trial. You’ve got to download it, jump through a load of hoops to set it up, and then have a call with a sales rep at HBXL.
From a functionality perspective, you need a Windows computer with Microsoft Excel installed. So, if you’re using Linux or IOS, you won’t be able to try this.
It can be buggy, too, and HBXL’s response to this is:
“Microsoft Office has become increasingly unstable within the last 18 months with numerous updates fundamentally altering the way Excel works and causing issues for all companies who provide Excel-based software programmes.”
While transparent, it’s perhaps not the most reassuring.
And since HBXL is Excel-based, don’t expect a modern and intuitive experience.
Verdict
HBXL is a great solution for those who cannot part with Excel spreadsheets, especially those who like to get into the granular detail of number crunching and analysing reports.
While expensive, there is an option for outright purchase, too, so if you try it and instinctively know this is the right software for you, then you may well benefit from committing to a one-time fee.
Summary
- Cost:
- EstimatorXpress Plus: £649/year
- EstimatorXpress Premium: £799/year
- EstimatorXpress Plus: £1,599 (outright purchase)
- EstimatorXpress Premium: £1,999 (outright purchase)
5. esti-mate
esti-mate provides a powerful piece of estimating software that can be used for all sizes and types of jobs, including small and large building projects and civil engineering work, as well as specialist trades. It’s a Windows-based program rather than cloud-based software.
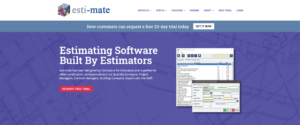
Pros
esti-mate software allows users to produce quotations, schedules, and traditional bill of quantities quickly and in a variety of ways, which can then be emailed or printed as a set of professional documents.
One handy feature is that groups of items can be rapidly located and displayed as a single list. Such grouping includes items that have not yet been priced, items containing selected resources, and items over a selected value.
It’s also incredibly easy to add, copy, or amend items.
Perhaps the most distinctive feature of esti-mate is the ability to add in waste factors for individual items or globally across all items, giving you greater control and visibility of costs to prevent overrun. This is the only software in this review that isolates and attributes a value to waste.
esti-mate also offers a true multi-user experience, meaning the program can be set to run in multi-user mode, allowing more than one user to view the same job at the same time—at no extra cost with no limits on the number of users.
While it would make an expensive platform for a small business, medium to larger companies would benefit from unlimited user access on a single licence.
Cons
Getting started with esti-mate is slow and cumbersome. If you’re looking to take them up on the offer of a 20-day free trial, don’t be fooled into thinking you can access the download right away despite the prompts on their website.
You’ll need to fill out a form and then hit “Download”. But even after that, you’ll be greeted with a pop-up message that says a member of the esti-mate team will be in touch.
esti-mate is also one of the most expensive options straight out of the box. The downloadable software costs £1,270 for a one-time purchase, but users are also encouraged to attend a two-day training course onsite (£1,900). It’s completely unaffordable for smaller firms, despite claims of the opposite on their website.
The software itself looks like a programme straight out of the '90s. This begs the question: if the front end looks dated, is the backend also being neglected?
You would hope that resources and capital are being poured in to fuel innovation, much like BuildPartner, which is developing automated plan-reading capabilities that would automatically produce a benchmark quotation based on a project’s plans.
With esti-mate, there is no mention on the website with regards to how often the pricing library is updated, so it’s reasonable to assume that prices are not live like BuildPartner’s or HBXL’s.
The software only runs on Windows, so again, Linux and iOS users have no choice but to look elsewhere, and it also means that those using Windows wouldn’t be able to switch to iOS at a later date (at least, not without having to find another estimating software programme to replace esti-mate.)
Verdict
esti-mate is overpriced for a seemingly dated programme. The software itself is expensive, and the steep learning curve requires one to two days of onsite training, costing up to £2,000. Any software that requires a period of consolidated training and study is likely to be unsuitable for small businesses.
Everything from the software programme to the website and its content seems frozen in time. Despite this, many industry professionals use it daily. The strongest draw is that it offers better value for money when used by multiple users, as there is no additional cost per user.
Still, esti-mate’s reputation is hard to validate, with only three unverified testimonials on its website and no reviews on Capterra or Trustpilot.
Summary
Best Pricing Tools for Construction Companies
When choosing the best estimation software, your main concern is the accuracy of cost estimation. Inaccurate software leads to cost overruns, so estimation software that uses a real-time database of prices and accurate estimations will help you win more bids and run more profitably. Take advantage of the free trials available at your disposal, starting with BuildPartner, of course.
Frequently Asked Questions About Construction Estimation Software
Below are some frequently asked questions about construction estimation software.
Is construction estimation software suitable for small businesses?
Yes, there are scalable solutions available that cater to small businesses, offering essential features without overwhelming complexity. The right software will simplify the process for small to medium businesses through automated calculations and itemised schedules, reducing the time spent on manual data entry and revisions.
What is Procore?
Procore is a comprehensive construction management software that offers tools for scheduling, document management, cost tracking, quality and safety monitoring, and mobile access. It’s generally suited to bigger construction companies quoting for projects over £1m.
Is Easy Price Pro still trading?
Build Aviator acquired the estimating software Easy Price Pro back in 2017. However, the software arm of Build Aviator closed in February 2024, and they now focus exclusively on providing estimating services. That means users of the software can no longer access the previous platforms, and any information published on the web regarding those (i.e., reviews and discussions) is now redundant.
What should I look for in construction estimation software?
Your main concern is the accuracy of cost estimation. Inaccurate software will lead to cost overruns. Estimation software that uses a real-time database of prices and accurate estimation templates will help you avoid overspending and ensure no key materials are missed due to human error.