May 28th, 2025
A garage conversion is a cost-effective way to add extra living space without the hassle of a full extension. But the costs vary depending on the room’s purpose; for instance, converting to a living room or utility room is usually more straightforward, while a new kitchen is more expensive due to plumbing and electrics and the need to install multiple appliances.
In this guide, we’ll break down the typical costs of converting your garage and how the total can vary depending on what you’re turning the space into. We’ll look at the cost of converting a garage by region and review average costs per square metre to help you budget accurately.
Garage Conversion Cost Calculations
The calculations in this guide assume that the existing structure remains in place, with no additional extensions. In terms of build specification, BuildPartner gives you three broad options to choose from:
- Basic spec is a basic finish; e.g., Leyland, Everest, Wickes.
- Standard spec is a standard finish; e.g., Dulux, Hamilton, Slim Line.
- Premium spec is a high-spec finish; e.g., Farrow & Ball, Fine Line, Siemens.
In this article, we’ve provided a breakdown of the cost of converting a garage to a standard specification. In addition, we have provided three different benchmarks to show the range of pricing you can expect among different contractors. These are:
- Low benchmark – smaller companies are generally lower cost but less specialised and with low project management function; good for low/mid-spec projects and tight budgets.
- Mid benchmark – medium-sized companies offer a balanced mix of cost-effectiveness and specialisation; good for mid-range projects for effective execution within moderate budgets.
- High benchmark – larger companies generally have a higher cost base but can handle a wide variety of specialist tasks; good for mid/high-spec projects and project management.
The costs in this guide are based on converting a double garage measuring 32m².
Cost Of Converting A Garage Into A Living Room
The table below shows the average cost of converting a double garage into a standard-spec living room:
Double Garage/Living Room (Standard Spec) |
Total Average Build Cost | Average Cost Per Sq Metre | ||||
Low Benchmark | Mid Benchmark | High Benchmark | Low Benchmark | Mid Benchmark | High Benchmark | |
East Anglia | £10,582 | £11,833 | £12,987 | £331 | £370 | £406 |
Greater London | £11,528 | £13,313 | £14,372 | £360 | £416 | £449 |
Inner London | £11,828 | £13,259 | £14,068 | £370 | £414 | £440 |
Midlands | £10,227 | £11,435 | £12,551 | £320 | £357 | £392 |
North England | £10,070 | £11,260 | £12,359 | £315 | £352 | £386 |
Northern Ireland | £10,381 | £11,203 | £12,604 | £321 | £350 | £394 |
Scotland | £10,492 | £11,732 | £12,876 | £328 | £367 | £402 |
South East | £10,489 | £11,636 | £13,012 | £356 | £395 | £437 |
South West | £10,378 | £11,918 | £13,081 | £333 | £372 | £409 |
Wales | £10,098 | £11,291 | £12,222 | £316 | £353 | £382 |
Average | £10,607 | £11,888 | £13,013 | £335 | £375 | £410 |
All costs exclude VAT.
Here’s what the data shows for the cost of converting a double garage into a standard-spec living room:
- It costs 10% more to convert a garage in Inner London.
- The minimum cost is £10,070, and the maximum cost is £14,372.
- The total average cost is £11,836, or £373 per square metre.
The costs in this example do not include those associated with relocating the boiler or hot water cylinders.
Start your free trial with BuildPartner to get a bespoke estimate of your construction project within minutes.
Cost Of Converting A Garage Into A Kitchen
The table below shows the average cost of converting a double garage into a standard-spec kitchen:
Double Garage/Kitchen (Standard Spec) |
Total Average Build Cost | Average Cost Per Sq Metre | ||||
Low Benchmark | Mid Benchmark | High Benchmark | Low Benchmark | Mid Benchmark | High Benchmark | |
East Anglia | £24,075 | £26,920 | £29,546 | £752 | £841 | £923 |
Greater London | £25,259 | £29,313 | £31,742 | £789 | £916 | £992 |
Inner London | £26,175 | £29,202 | £30,344 | £818 | £913 | £948 |
Midlands | £23,565 | £26,350 | £28,921 | £736 | £823 | £904 |
North England | £23,304 | £26,058 | £28,600 | £728 | £814 | £894 |
Northern Ireland | £23,979 | £25,923 | £29,163 | £743 | £810 | £911 |
Scotland | £24,196 | £27,056 | £29,695 | £756 | £845 | £928 |
South East | £23,164 | £25,794 | £28,429 | £787 | £876 | £966 |
South West | £23,743 | £27,009 | £29,644 | £755 | £844 | £926 |
Wales | £23,332 | £26,089 | £27,957 | £729 | £815 | £874 |
Average | £24,079 | £26,971 | £29,404 | £759 | £850 | £927 |
All costs exclude VAT.
Here’s what the data shows for the cost of converting a double garage into a standard-spec kitchen:
- The minimum cost is £23,164, and the maximum cost is £31,742.
- The total average cost is £26,818, or £845 per square metre.
This includes appliances such as an electric hob, extractor fan, oven, fridge, freezer, dishwasher, tumble dryer, washing machine, worktops, and a sink. It doesn’t include costs associated with relocating the boiler or hot water cylinders.
Cost Of Converting A Garage Into A Utility Room
The table below shows the average cost of converting a double garage into a standard-spec utility room:
Double Garage/Utility Room (Standard Spec) |
Total Average Build Cost | Average Cost Per Sq Metre | ||||
Low Benchmark | Mid Benchmark | High Benchmark | Low Benchmark | Mid Benchmark | High Benchmark | |
East Anglia | £12,199 | £13,641 | £14,972 | £381 | £426 | £468 |
Greater London | £13,087 | £15,170 | £16,315 | £409 | £474 | £510 |
Inner London | £13,487 | £15,091 | £15,923 | £421 | £472 | £498 |
Midlands | £11,808 | £13,203 | £14,491 | £369 | £413 | £453 |
North England | £11,621 | £12,994 | £14,262 | £363 | £406 | £446 |
Northern Ireland | £11,388 | £12,734 | £13,977 | £356 | £398 | £437 |
Scotland | £12,179 | £13,619 | £14,947 | £381 | £426 | £467 |
South East | £11,965 | £13,276 | £14,844 | £374 | £415 | £464 |
South West | £11,956 | £13,697 | £15,033 | £374 | £428 | £470 |
Wales | £11,663 | £13,042 | £14,074 | £364 | £408 | £440 |
Average | £12,135 | £13,647 | £14,884 | £379 | £426 | £465 |
All costs exclude VAT.
Here’s what the data shows for the cost of converting a double garage into a standard-spec utility room:
- The minimum cost is £11,388, and the maximum cost is £16,315.
- The total average cost is £13,555, or £424 per square metre.
This includes worktops, a sink, a tumble dryer, and a washing machine. It doesn’t include costs associated with relocating the boiler or hot water cylinders.
Average Cost Of Converting A Garage
So, how much does it cost to convert a garage in the UK? Based on the three types of garage conversions covered in this article, it costs on average (when using a mid-benchmark contractor):
- Double Garage to a Living Room: £11,888, or £375 per square metre.
- Double Garage to a Utility Room: £13,647, or £426 per square metre.
- Double Garage to a Kitchen: £26,971, or £850 per square metre.
If you’re converting a single garage, simply use the cost per square metre outlined for double garages and adjust based on the size of your space to get a ballpark figure.
Start your free trial with BuildPartner to get a bespoke estimate of your construction project within minutes.
Please remember that all costs exclude VAT.
Frequently Asked Questions About Garage Conversions
Explore answers to frequently asked questions about garage conversions.
Will a garage conversion add value to my home?
A garage conversion can increase a property’s value, sometimes by 10–20%, particularly if it creates additional living space such as a bedroom or office. Due to the rise of working from home, many buyers are now looking for exclusive office space.
In areas where off-street parking is limited, some buyers appreciate the security a garage offers. But if the property already has a driveway, the garage may surplus to requirements.
So a conversion can make far better use of the existing space, turning what might otherwise become a dumping ground for old boxes into a functional room.
Do I need building regulations approval for a garage conversion?
Building control must inspect and sign off on the project, which is usually handled by your local authority to ensure that the work meets safety and structural standards.
To convert a garage into living space, you don’t need planning permission as long as the work is internal and doesn’t involve enlarging the structure.
What types of rooms can a garage be converted into?
You can turn a garage into all sorts of useful spaces, depending on what you need. Popular choices include an extra bedroom, home office, playroom, gym, utility room, living room, or even a kitchen or bathroom.
Some options are pretty straightforward, like a bedroom or office, but if you plan to put in a kitchen or bathroom, the costs will be higher, since you’ll need to factor in the cost of plumbing, electrical work, and appliances.
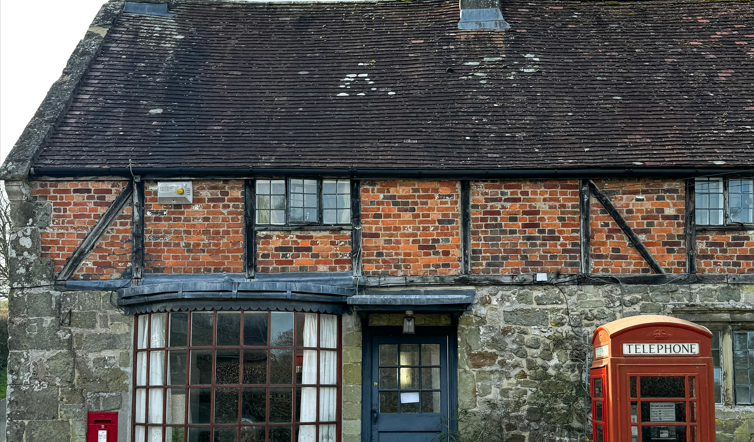
May 28th, 2025
Most houses in the UK are still built with brick, but there is a growing trend towards timber due to its environmental benefits and build efficiency, with around 23% of new homes built being with timber and a whopping 85% in Scotland!
In addition, the UK Government has published a roadmap that outlines efforts to increase timber use in construction, aiming to meet net-zero targets. So, with a growing trend, important to understand cost implications.
In this guide, we’ll break down the typical costs of building a timber-frame home versus a brick/block home. We’ll look at the cost of building by region and review average costs per square metre to help you budget accurately.
Brick & Timber Frame Cost Calculations
In terms of build specification, BuildPartner gives you three broad options to choose from:
- Basic spec is a basic finish; e.g., Leyland, Everest, Wickes.
- Standard spec is a standard finish; e.g., Dulux, Hamilton, Slim Line.
- Premium spec is a high-spec finish; e.g., Farrow & Ball, Fine Line, Siemens.
In this article, we’ve provided a breakdown of the cost of converting a garage to a standard specification. In addition, we have provided three different benchmarks to show the range of pricing you can expect among different contractors. These are:
- Low benchmark – smaller companies are generally lower cost but less specialised and with low project management function; good for low/mid-spec projects and tight budgets.
- Mid benchmark – medium-sized companies offer a balanced mix of cost-effectiveness and specialisation; good for mid-range projects for effective execution within moderate budgets.
- High benchmark – larger companies generally have a higher cost base but can handle a wide variety of specialist tasks; good for mid/high-spec projects and project management.
The costs in this guide are based on building a two-storey home comprising 95m². The figures cover the cost of constructing the external shell only and exclude internal finishes, such as kitchens, bathrooms, and flooring.
Cost Of Building A Timber Home
The table below shows the average cost of building a home using a timber frame:
3-Bed Detached - Timber | Total Average Build Cost | Average Cost Per Sq Metre | ||||
Low Benchmark | Mid Benchmark | High Benchmark | Low Benchmark | Mid Benchmark | High Benchmark | |
East Anglia | £194,352 | £217,320 | £238,522 | £2,046 | £2,288 | £2,511 |
Greater London | £211,159 | £244,465 | £256,137 | £2,223 | £2,573 | £2,696 |
Inner London | £215,059 | £242,501 | £252,841 | £2,264 | £2,553 | £2,661 |
Midlands | £188,611 | £210,901 | £231,477 | £1,985 | £2,220 | £2,437 |
North England | £185,031 | £206,898 | £227,084 | £1,948 | £2,178 | £2,390 |
Northern Ireland | £190,391 | £206,454 | £232,261 | £1,992 | £2,173 | £2,445 |
Scotland | £191,532 | £214,167 | £235,062 | £2,016 | £2,254 | £2,474 |
South East | £190,779 | £212,155 | £236,683 | £2,183 | £2,427 | £2,679 |
South West | £190,748 | £221,309 | £242,935 | £2,084 | £2,330 | £2,557 |
Wales | £183,549 | £205,242 | £221,042 | £1,932 | £2,160 | £2,327 |
Average | £194,121 | £218,141 | £237,404 | £2,067 | £2,316 | £2,518 |
All costs exclude VAT.
Here’s what the data shows for the cost of building a home with a timber frame:
- It costs 9% more to build a timber-framed home in Inner London.
- The minimum cost is £183,549, and the maximum cost is £256,137.
- The total average cost is £216,556, or £2,300 per square metre.
Start your free trial with BuildPartner to get a bespoke estimate of your construction project within minutes.
Cost Of Building A Brick/Block Home
The table below shows the average cost of building a home using brick/block:
3-Bed Detached - Brick/Block | Total Average Build Cost | Average Cost Per Sq Metre | ||||
Low Benchmark | Mid Benchmark | High Benchmark | Low Benchmark | Mid Benchmark | High Benchmark | |
East Anglia | £193,292 | £216,135 | £237,222 | £2,035 | £2,275 | £2,497 |
Greater London | £208,178 | £246,594 | £253,233 | £2,191 | £2,596 | £2,666 |
Inner London | £210,823 | £238,631 | £247,456 | £2,219 | £2,512 | £2,605 |
Midlands | £187,235 | £209,363 | £229,789 | £1,971 | £2,204 | £2,419 |
North England | £181,899 | £203,396 | £223,239 | £1,915 | £2,141 | £2,350 |
Northern Ireland | £186,692 | £203,383 | £228,806 | £1,962 | £2,141 | £2,408 |
Scotland | £186,949 | £209,043 | £229,437 | £1,968 | £2,200 | £2,415 |
South East | £188,007 | £209,058 | £230,735 | £2,151 | £2,392 | £2,640 |
South West | £188,933 | £219,603 | £241,063 | £2,068 | £2,312 | £2,538 |
Wales | £181,444 | £202,888 | £218,388 | £1,910 | £2,136 | £2,299 |
Average | £191,345 | £215,809 | £233,937 | £2,039 | £2,291 | £2,484 |
All costs exclude VAT.
Here’s what the data shows for the cost of building a home using brick/block:
- The minimum cost is £181,444, and the maximum cost is £253,233.
- The total average cost is £213,697, or £2,271 per square metre.
Comparison Of Stages
The table below shows the costs associated with the different stages of the two types of construction methods:
Timber | Brick/Block | |||||
Total | £242,501 | 100.0% | Total | £238,631 | 98.4% | |
External wall structure and lining | £64,085 | 26.4% | External wall structure and lining | £61,560 | 25.4% | |
Foundations and substructure | £38,429 | 15.8% | Foundations and substructure | £38,429 | 15.8% | |
Roof structure and coverings | £35,192 | 14.5% | Roof structure and coverings | £35,192 | 14.5% | |
Preliminaries | £32,233 | 13.3% | Preliminaries | £34,414 | 14.2% | |
Floor structure and lining | £24,576 | 10.1% | Floor structure and lining | £21,402 | 8.8% | |
Drainage and pipework | £15,036 | 6.2% | Drainage and pipework | £15,050 | 6.2% | |
Internal wall structure and lining | £13,167 | 5.4% | Internal wall structure and lining | £13,167 | 5.4% | |
Steel and structural supports | £10,762 | 4.4% | Steel and structural supports | £10,396 | 4.3% | |
Ceiling structure and lining | £3,995 | 1.6% | Ceiling structure and lining | £3,995 | 1.6% | |
Wiring and fuseboards | £2,777 | 1.1% | Wiring and fuseboards | £2,777 | 1.1% | |
Demolitions | £1,373 | 0.6% | Demolitions | £1,373 | 0.6% | |
Heating and cooling | £877 | 0.4% | Heating and cooling | £877 | 0.4% |
All costs exclude VAT.
- The total cost for the timber build is £242,501, compared to £238,631 for brick/block—making timber about 1.6% more expensive overall.
- External wall structure and lining cost £64,085 (26.4%) for timber, versus £61,560 (25.4%) for brick/block, indicating higher material and fabrication costs for timber frames.
- The floor structure and lining is less expensive in the brick/block build at £21,402 (8.8%), compared to £24,576 (10.1%) in the timber version.
Comparison Of Elements
The table below shows the costs associated with the different elements of the two types of construction methods:
Timber | Brick/Block | |||||
Total | £242,501 | 100% | Total | £238,631 | 100% | |
External wall lining | £26,972 | 11.1% | External wall structure | £48,999 | 20.5% | |
External wall finishes | £21,020 | 8.7% | External wall finishes | £ - | 0.0% | |
Foundations | £19,726 | 8.1% | Project management | £20,595 | 8.6% | |
Project management | £18,532 | 7.6% | Foundations | £19,726 | 8.3% | |
Floor structure | £18,130 | 7.5% | Floor structure | £14,955 | 6.3% | |
External wall structure | £16,093 | 6.6% | External wall lining | £12,560 | 5.3% | |
Roof lining | £12,396 | 5.1% | Roof lining | £12,396 | 5.2% | |
Structural supports | £10,332 | 4.3% | Internal wall structure | £10,167 | 4.3% | |
Internal wall structure | £10,167 | 4.2% | Roof coverings | £10,014 | 4.2% | |
Roof coverings | £10,014 | 4.1% | Structural supports | £9,966 | 4.2% | |
Excavation | £9,732 | 4.0% | Excavation | £9,732 | 4.1% | |
Roof structure | £9,263 | 3.8% | Roof structure | £9,263 | 3.9% | |
Scaffolding | £7,050 | 2.9% | Scaffolding | £7,050 | 3.0% | |
Waste pipework | £6,486 | 2.7% | Waste pipework | £6,486 | 2.7% | |
Floor lining | £6,447 | 2.7% | Floor lining | £6,447 | 2.7% | |
Hardcore | £4,938 | 2.0% | Hardcore | £4,938 | 2.1% | |
Rainwater drainage | £4,447 | 1.8% | Rainwater drainage | £4,461 | 1.9% | |
Ceiling lining | £3,995 | 1.6% | Ceiling lining | £3,995 | 1.7% | |
Internal wall lining | £2,999 | 1.2% | Internal wall lining | £2,999 | 1.3% | |
Access points | £2,866 | 1.2% | Access points | £2,866 | 1.2% | |
Waste disposal | £2,304 | 1.0% | Waste disposal | £2,304 | 1.0% | |
Fascias | £2,250 | 0.9% | Fascias | £2,250 | 0.9% | |
Reinforcement | £2,170 | 0.9% | Reinforcement | £2,170 | 0.9% | |
Cabling | £1,732 | 0.7% | Cabling | £1,732 | 0.7% | |
Machinery / Equipment | £1,632 | 0.7% | Machinery / Equipment | £1,632 | 0.7% | |
Light demolition | £1,373 | 0.6% | Light demolition | £1,373 | 0.6% | |
Blinding | £1,263 | 0.5% | Blinding | £1,263 | 0.5% | |
Hot and cold pipework | £1,237 | 0.5% | Utilities | £1,243 | 0.5% | |
Utilities | £1,126 | 0.5% | Hot and cold pipework | £1,237 | 0.5% | |
Pipework | £877 | 0.4% | Pipework | £877 | 0.4% | |
Hoarding | £857 | 0.4% | Hoarding | £857 | 0.4% | |
General allowances | £732 | 0.3% | General allowances | £732 | 0.3% | |
Fuseboards | £723 | 0.3% | Fuseboards | £723 | 0.3% | |
Flashing | £626 | 0.3% | Flashing | £626 | 0.3% | |
Damp proofing | £601 | 0.2% | Damp proofing | £601 | 0.3% | |
Bargeboards | £541 | 0.2% | Bargeboards | £541 | 0.2% | |
Padstones | £430 | 0.2% | Padstones | £430 | 0.2% | |
Electrical certification | £321 | 0.1% | Electrical certification | £321 | 0.1% | |
Roof ventilation | £102 | 0.0% | Roof ventilation | £102 | 0.0% |
Here are the key takeaways from the cost comparison between timber and brick/block construction:
- Brick/block spends £48,999 (20.5%) on external wall structure—almost double the £25,972 (11.1%) spent in the timber build. However, timber allocates more to internal wall components and finishes.
- No budget is allocated for brick/block for external wall finishes, while timber includes £21,020 for finishes. The brick façade is structural and finish in one, while timber needs cladding added separately.
- Timber shows higher costs in project management (£18,532 vs £15,395) and floor structure (£18,130 vs £14,596) due to the complexity of assembling prefabricated components on site.
- Several elements, such as scaffolding, roof structure, ceiling lining, access points, and fascias, have the exact same costs, showing standardisation across both methods for these elements.
- Timber spends slightly more on roof coverings, floor lining, and internal wall structure, indicating a focus on finish quality and extra insulation needs.
Average Cost Of Building With Brick & Timber
So, what’s the average cost difference of building with brick/block versus timber in the UK? Based on building a two-storey property comprising 95m2, it costs on average (when using a mid-benchmark contractor):
- Two-storey timber-frame build: £218,141, or £2,316 per square metre.
- Two-storey brick/block build: £215,809, or £2,291 per square metre.
So, overall in the housing sector, timber and masonry builds show near price parity once all construction factors are taken into account.
Start your free trial with BuildPartner to get a bespoke estimate of your construction project within minutes.
Please remember that all costs exclude VAT.
Frequently Asked Questions About Building With Brick & Timber
Explore answers to frequently asked questions about building with brick/block and timber.
What are the benefits of building with brick and timber?
Brick has a higher thermal mass, meaning it retains heat during the day and releases it slowly, which helps keep your home warm in winter and cooler in summer. It’s also great at blocking out noise, which is great if you live near a road or in a busy area. In addition, brick doesn’t need much looking after and tends to outlast alternatives like timber cladding.
Timber is much better for the environment, with a much lower carbon footprint than brick. It also offers lots of design options, from precise geometrical shells to a variety of looks including clean, contemporary, rustic, traditional, and weathered. It can be quicker to work with, especially if you’re using prefabricated sections.
Are there any fire safety concerns when using timber frames?
Timber is a combustible material, whereas brick and block are non-combustible and therefore fire-resistant. So, fire safety must be carefully planned. Quite often, engineered timber is used, which chars predictably and maintains structural integrity longer when exposed to heat and flames.
Building Regulations typically require additional fire safety measures such as fire-rated cladding, treated timber, and internal fire doors. While sprinklers are only mandared on domestic buildings over 4 storeys or in Wales for new-builds, it’s still a good idea to install them.
How durable is brick and timber construction?
Brick is extremely durable and can last over 100 years with minimal maintenance; it’s also resistant to fire, pests (insects such as woodlice), and weather.
On average, you can expect to replace timber cladding every 20 to 40 years depending on the climate and the type of wood (hardwoods like oak typically last longer than softwoods like pine). If the property is in a damp, coastal, or harsh climate, the timber cladding is likely to need replacing sooner due to exposure to moisture, salt, and weathering.
Why does timber need careful storage on site?
Timber needs to be carefully stored on site unlike brick/block. Once it’s delivered, you’ve got to keep it dry and properly protected. Too much moisture causes warping (especially without airflow), and if it’s not stacked right, it can bend and get scratched.
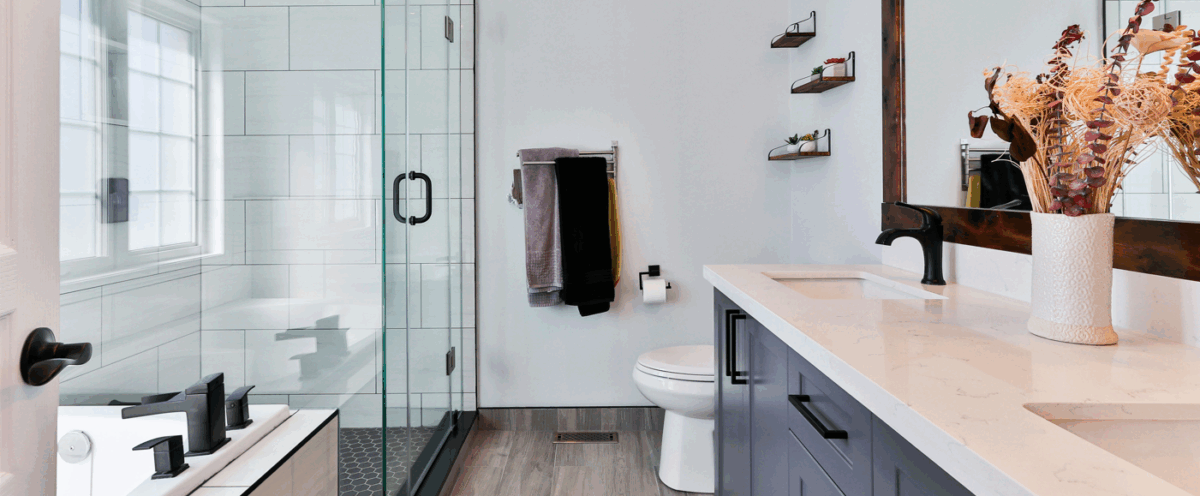
April 28th, 2025
From tiling and plumbing to fixtures and finishes, the costs to renovate a bathroom renovation vary widely depending on the size of the space and the specifications of the project. This guide breaks down typical bathroom renovation costs in the UK so that you can plan your budget with no nasty surprises.
We look at the cost of fully renovating three common bathroom types: a main bathroom, an ensuite, and a WC. We also break down average renovation costs by UK region and per square metre. One notable exclusion is underfloor heating, as it’s not always essential.
Bathroom Renovation Cost Calculations
In terms of build specification, BuildPartner gives you three broad options to choose from:
- Basic spec is a basic finish; e.g., Leyland, Everest, Wickes.
- Standard spec is a standard finish; e.g., Dulux, Hamilton, Slim Line.
- Premium spec is a high-spec finish; e.g., Farrow & Ball, Fine Line, Siemens.
In this article, we provide a breakdown of the cost of renovating a bathroom for all three specifications. In addition to this, we also provide three different benchmarks to show the range of pricing you can expect among different contractors. These are:
- Low benchmark – smaller companies are generally lower cost but less specialised and with low project management function; good for low/mid-spec projects and tight budgets.
- Mid benchmark – medium-sized companies offer a balanced mix of cost-effectiveness and specialisation; good for mid-range projects for effective execution within moderate budgets.
- High benchmark – larger companies generally have a higher cost base but can handle a wide variety of specialist tasks; good for mid/high-spec projects and project management.
Average Cost Of A Bathroom Renovation (Standard Spec)
The table below shows the average cost of renovating a bathroom in the UK to a standard spec:
Bathroom Renovation (Standard Spec) |
Total Average Build Cost | Average Cost Per Sq Metre | ||||
Low Benchmark | Mid Benchmark | High Benchmark | Low Benchmark | Mid Benchmark | High Benchmark | |
East Anglia | £9,292 | £10,390 | £11,404 | £1,549 | £1,732 | £1,901 |
Greater London | £9,757 | £11,151 | £11,983 | £1,626 | £1,858 | £1,997 |
Inner London | £10,000 | £11,162 | £11,627 | £1,667 | £1,860 | £1,938 |
Midlands | £8,959 | £10,018 | £10,996 | £1,493 | £1,670 | £1,833 |
North England | £8,801 | £9,842 | £10,802 | £1,467 | £1,640 | £1,800 |
Northern Ireland | £9,116 | £9,930 | £11,171 | £1,517 | £1,655 | £1,862 |
Scotland | £9,129 | £10,208 | £11,204 | £1,522 | £1,701 | £1,867 |
South East | £8,925 | £9,863 | £11,072 | £1,617 | £1,787 | £1,984 |
South West | £9,088 | £10,410 | £11,425 | £1,552 | £1,735 | £1,904 |
Wales | £8,866 | £9,914 | £10,636 | £1,478 | £1,652 | £1,773 |
Average | £9,193 | £10,289 | £11,232 | £1,549 | £1,729 | £1,886 |
All costs exclude VAT.
Here’s what the data shows for the cost of renovating a bathroom to a standard spec:
- It costs 7% more to renovate a bathroom in Inner London.
- The minimum cost is £8,801, and the maximum cost is £11,983.
- The total average cost is £10,238, or £1,721 per square metre.
Start your free trial with BuildPartner to get a bespoke estimate of your construction project within minutes.
Bathroom Renovation Cost Breakdown By Project Stage – London
Here’s an example of the associated costs for the different stages of renovating a bathroom for a standard-spec project – when using a mid-benchmark contractor in London:
Total | £11,162 | 100% |
Plumbed appliances | £3,939 | 35.3% |
Wall preparation and finishes | £2,345 | 21.0% |
Floor preparation and finishes | £1,563 | 14.0% |
Decoration | £1,184 | 10.6% |
Wired appliances | £809 | 7.2% |
Fixtures and fittings | £444 | 4.0% |
Heating and cooling | £336 | 3.0% |
Demolitions | £275 | 2.5% |
Preliminaries | £221 | 2.0% |
Ceiling preparation and finishes | £47 | 0.4% |
Average Cost Of An Ensuite Bathroom Renovation (Standard Spec)
The table below shows the average cost of renovating an ensuite bathroom in the UK to a standard spec:
All costs exclude VAT. Here’s what the data shows for the cost of renovating an ensuite bathroom to a standard spec:
- The minimum cost is £6,296, and the maximum cost is £9,644.
- The total average cost is £8,104, or £2,181 per square metre.
The table below shows the average cost of renovating an ensuite bathroom in the UK to a standard spec:
En-Suite Renovation (Standard Spec) |
Total Average Build Cost | Average Cost Per Sq Metre | ||||
Low Benchmark | Mid Benchmark | High Benchmark | Low Benchmark | Mid Benchmark | High Benchmark | |
East Anglia | £7,352 | £8,221 | £9,023 | £1,961 | £2,192 | £2,406 |
Greater London | £7,776 | £8,959 | £9,644 | £2,074 | £2,389 | £2,572 |
Inner London | £7,941 | £8,865 | £9,268 | £2,118 | £2,364 | £2,472 |
Midlands | £7,061 | £7,895 | £8,665 | £1,883 | £2,105 | £2,311 |
North England | £6,926 | £7,745 | £8,500 | £1,847 | £2,065 | £2,267 |
Northern Ireland | £7,203 | £7,826 | £8,805 | £1,913 | £2,087 | £2,348 |
Scotland | £7,231 | £8,086 | £8,875 | £1,928 | £2,156 | £2,367 |
South East | £7,090 | £7,834 | £8,701 | £2,055 | £2,271 | £2,522 |
South West | £7,175 | £8,245 | £9,050 | £1,966 | £2,199 | £2,413 |
Wales | £6,976 | £7,800 | £8,379 | £1,860 | £2,080 | £2,235 |
Average | £7,273 | £8,148 | £8,891 | £1,960 | £2,191 | £2,391 |
All costs exclude VAT.
Here’s what the data shows for the cost of renovating an ensuite bathroom to a standard spec:
- The minimum cost is £6,296, and the maximum cost is £9,644.
- The total average cost is £8,104, or £2,181 per square metre.
Average Cost Of A WC Renovation (Standard Spec)
The table below shows the average cost of renovating a WC in the UK to a standard spec:
WC Renovation (Standard Spec) |
Total Average Build Cost | Average Cost Per Sq Metre | ||||
Low Benchmark | Mid Benchmark | High Benchmark | Low Benchmark | Mid Benchmark | High Benchmark | |
East Anglia | £3,071 | £3,434 | £3,769 | £1,422 | £1,590 | £1,745 |
Greater London | £3,274 | £3,759 | £4,027 | £1,516 | £1,740 | £1,864 |
Inner London | £3,354 | £3,744 | £3,946 | £1,553 | £1,733 | £1,827 |
Midlands | £2,949 | £3,297 | £3,619 | £1,365 | £1,526 | £1,675 |
North England | £2,896 | £3,239 | £3,555 | £1,341 | £1,499 | £1,646 |
Northern Ireland | £2,838 | £3,174 | £3,483 | £1,314 | £1,469 | £1,613 |
Scotland | £3,019 | £3,375 | £3,705 | £1,397 | £1,563 | £1,715 |
South East | £2,992 | £3,310 | £3,712 | £1,385 | £1,532 | £1,719 |
South West | £3,003 | £3,446 | £3,782 | £1,390 | £1,595 | £1,751 |
Wales | £2,924 | £3,270 | £3,524 | £1,354 | £1,514 | £1,631 |
Average | £3,032 | £3,405 | £3,712 | £1,404 | £1,576 | £1,719 |
All costs exclude VAT.
Here’s what the data shows for the cost of renovating a WC to a standard spec:
- The minimum cost is £2,838, and the maximum cost is £4,027.
- The total average cost is £3,383, or £1,566 per square metre.
Average Cost Of Renovating A Bathroom
So, how much does it cost to renovate a bathroom in the UK? Based on the three specifications covered in this article, you can expect a bathroom renovation to cost on average (when using a mid-benchmark contractor):
- Bathroom: £10,289, or £1,729 per square metre.
- En-suite: £8,148, or £2,191 per square metre.
- WC: £3,405, or £1,576 per square metre.
Please remember that all costs exclude VAT.
Start your free trial with BuildPartner to get a bespoke estimate of your construction project within minutes.
Frequently Asked Questions About Bathroom Renovation Costs
Here are some frequently asked questions about bathroom renovation costs.
Does changing the bathroom layout increase the cost?
Any deviation from the existing layout pushes up labour costs and extends the schedule. For example, moving a toilet typically involves relocating the soil pipe, which may mean breaking up floors or boxing in new pipe runs.
Similarly, relocating a shower or bath means installing new hot and cold feeds, as well as drainage. Not only that, but structural changes, like moving a wall or window, bring in additional trades such as joiners and bricklayers.
How can I keep costs low when renovating a bathroom?
There are plenty of ways to keep costs under control. The biggest saver is sticking to the existing layout. Keeping toilets, showers, and basins in the same position avoids the need to move pipework.
Also, you don’t need to tile every wall — just the wet areas and a splashback behind the basin. The rest can be plastered and painted with good-quality anti-condensation paint.
If the existing toilet or basin is in decent condition, you might be able to keep it and just replace the taps or seat. With a bit of effort, ceramic surfaces clean up nicely.
How much space do I need for an ensuite?
You can fit a compact ensuite into as little as 1.5m x 1m using space-saving fixtures like corner basins and sliding doors. It won’t be spacious, but it’ll be functional. A typical ensuite is usually around 1.5m x 2.5m (3.75m²), giving enough space for a toilet, basin, and shower.
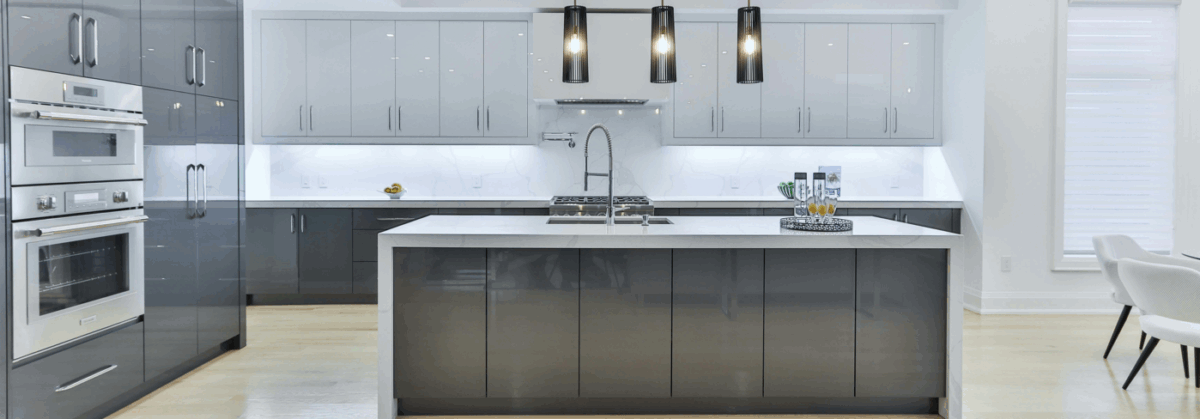
April 28th, 2025
If you’re planning to remodel your existing space to make way for an open-plan kitchen diner, the total cost can vary widely depending on factors such as the specification, local labour rates, structural work required, and the quality of materials you choose.
In this article, we cover the costs involved in converting your existing kitchen and living room, typically by downsizing the living space, to create a larger, open-plan kitchen diner. From knocking down walls and moving utilities to choosing your units and finishes, we’ll break down what you can expect to spend.
We’ll take a look at the cost of converting a kitchen diner by region, covering London, North England, Scotland, Wales, and Northern Ireland. We’ll also review average costs per square metre to help you budget accurately and avoid overspending.
Kitchen Diner Cost Calculations
The calculations in this guide assume that the existing structure remains in place, with no additional extensions. The cost breakdown includes a full kitchen remodel with all-new appliances—hob, electric oven, fridge, freezer, dishwasher, washing machine, and extractor fan.
It also includes the installation of bifold doors to open up the space between inside and outside for a blended dining experience.
In terms of build specification, BuildPartner gives you three broad options to choose from:
- Basic spec is a basic finish; e.g., Leyland, Everest, Wickes.
- Standard spec is a standard finish; e.g., Dulux, Hamilton, Slim Line.
- Premium spec is a high-spec finish; e.g., Farrow & Ball, Fine Line, Siemens.
In this article, we’ve provided a breakdown of the cost of converting to a kitchen diner for all three specifications. In addition to this, we have also provided three different benchmarks to show the range of pricing you can expect among different contractors. These are:
- Low benchmark – smaller companies are generally lower cost but less specialised and with low project management function; good for low/mid-spec projects and tight budgets.
- Mid benchmark – medium-sized companies offer a balanced mix of cost-effectiveness and specialisation; good for mid-range projects for effective execution within moderate budgets.
- High benchmark – larger companies generally have a higher cost base but can handle a wide variety of specialist tasks; good for mid/high-spec projects and project management.
Cost Of Kitchen Diner Conversion (Basic Spec)
Below is a table showing the average cost of converting a kitchen diner in the UK to a basic spec:
Kitchen Diner Conversion (Basic Spec) |
Total Average Build Cost | Average Cost Per Sq Metre | ||||
Low Benchmark | Mid Benchmark | High Benchmark | Low Benchmark | Mid Benchmark | High Benchmark | |
East Anglia | £25,792 | £28,840 | £31,654 | £614 | £687 | £754 |
Greater London | £27,470 | £32,271 | £34,396 | £654 | £768 | £819 |
Inner London | £28,390 | £31,780 | £33,296 | £676 | £757 | £793 |
Midlands | £25,026 | £27,983 | £30,714 | £596 | £666 | £731 |
North England | £24,598 | £27,505 | £30,189 | £586 | £655 | £719 |
Northern Ireland | £25,722 | £27,934 | £31,425 | £610 | £665 | £748 |
Scotland | £25,839 | £28,892 | £31,711 | £615 | £688 | £755 |
South East | £25,169 | £28,108 | £31,225 | £651 | £727 | £799 |
South West | £25,301 | £29,056 | £31,900 | £619 | £692 | £760 |
Wales | £24,610 | £27,518 | £29,602 | £586 | £655 | £705 |
Average | £25,792 | £28,989 | £31,611 | £621 | £696 | £758 |
All costs exclude VAT.
Here’s what the data shows for the cost of converting a kitchen diner to a basic spec:
- It costs 8% more to convert a kitchen diner in Inner London.
- The minimum cost is £24,598, and the maximum cost is £34,396.
- The total average cost is £28,797, or £692 per square metre.
Start your free trial with BuildPartner to get a bespoke estimate of your construction project within minutes.
Cost Of Kitchen Diner Conversion (Standard Spec)
The table below shows the average cost of converting a kitchen diner in the UK to a standard spec:
Kitchen Diner Conversion (Standard Spec) |
Total Average Build Cost | Average Cost Per Sq Metre | ||||
Low Benchmark | Mid Benchmark | High Benchmark | Low Benchmark | Mid Benchmark | High Benchmark | |
East Anglia | £33,824 | £37,821 | £41,511 | £805 | £900 | £988 |
Greater London | £35,516 | £41,339 | £44,519 | £846 | £984 | £1,060 |
Inner London | £36,787 | £41,154 | £42,611 | £876 | £980 | £1,015 |
Midlands | £33,058 | £36,964 | £40,571 | £787 | £880 | £966 |
North England | £32,630 | £36,486 | £40,046 | £777 | £869 | £953 |
Northern Ireland | £33,754 | £36,695 | £41,282 | £801 | £874 | £983 |
Scotland | £33,870 | £37,873 | £41,568 | £806 | £902 | £990 |
South East | £32,559 | £36,260 | £39,958 | £843 | £938 | £1,034 |
South West | £33,333 | £38,037 | £41,757 | £810 | £906 | £994 |
Wales | £32,641 | £36,499 | £39,094 | £777 | £869 | £931 |
Average | £33,797 | £37,913 | £41,292 | £813 | £910 | £991 |
All costs exclude VAT.
Here’s what the data shows for the cost of converting a kitchen diner to a standard spec:
- The minimum cost is £32,559, and the maximum cost is £44,519.
- The total average cost is £37,667, or £905 per square metre.
Cost Of Kitchen Diner Conversion (Premium Spec)
The table below shows the average cost of converting a kitchen diner in the UK to a premium spec:
Kitchen Diner Conversion (Premium Spec) |
Total Average Build Cost | Average Cost Per Sq Metre | ||||
Low Benchmark | Mid Benchmark | High Benchmark | Low Benchmark | Mid Benchmark | High Benchmark | |
East Anglia | £47,457 | £53,066 | £58,243 | £1,130 | £1,263 | £1,387 |
Greater London | £49,136 | £57,851 | £60,985 | £1,170 | £1,377 | £1,452 |
Inner London | £51,041 | £57,018 | £58,475 | £1,215 | £1,358 | £1,392 |
Midlands | £46,691 | £52,209 | £57,303 | £1,112 | £1,243 | £1,364 |
North England | £46,264 | £51,731 | £56,778 | £1,102 | £1,232 | £1,352 |
Northern Ireland | £45,338 | £50,697 | £55,643 | £1,079 | £1,207 | £1,325 |
Scotland | £47,504 | £53,118 | £58,300 | £1,131 | £1,265 | £1,388 |
South East | £45,102 | £50,396 | £55,954 | £1,074 | £1,200 | £1,332 |
South West | £46,966 | £53,282 | £58,489 | £1,118 | £1,269 | £1,393 |
Wales | £46,275 | £51,744 | £55,207 | £1,102 | £1,232 | £1,314 |
Average | £47,177 | £53,111 | £57,538 | £1,123 | £1,265 | £1,370 |
All costs exclude VAT.
Here’s what the data shows for the cost of converting a kitchen diner to a premium spec:
- The minimum cost is £45,102, and the maximum cost is £60,985.
- The total average cost is £52,609, or £1,253 per square metre.
Average Cost Of Converting A Kitchen Diner
So, how much does it cost to convert to a kitchen diner in the UK? Based on the three specifications covered in this article, you can expect a kitchen diner conversion to cost on average (when using a mid-benchmark contractor):
- Basic spec: £28,989, or £696 per square metre.
- Standard spec: £37,913, or £910 per square metre.
- Premium spec: £53,111, or £1,265 per square metre.
The costs in this guide exclude extensions. If you’re planning to build an extension to increase the floorspace of your kitchen diner, you should factor in approximately £2,900 per square metre for a ground-floor extension, and £2,400 for a double-storey rear extension.
For more specific information about extension costs, check out this article.
Please remember that all costs exclude VAT.
Start your free trial with BuildPartner to get a bespoke estimate of your construction project within minutes.
Frequently Asked Questions About Kitchen Diner Conversions
Here are some frequently asked questions about the costs of converting a kitchen diner.
How long does it take to convert a kitchen diner?
Converting to a kitchen diner takes an average of 3.75 weeks, with an average of two tradespeople carrying out the work. Here’s a rough breakdown of the project:
- Demolitions begin in Week 1 and wrap up by early Week 2.
- Windows and doors are installed in Week 1, followed by internal doors and frames.
- Drainage and pipework start in Week 2, overlapping with heating and cooling.
- Wired appliances are set up in Week 3, alongside ceiling and wall preparation.
- Worktops and kitchen appliances are installed in Week 4.
- Decoration begins in Week 4 and finishes in Week 5, marking the project’s end.
Can I knock through a wall to open up space for a kitchen diner?
Yes, if the wall isn’t load-bearing, it’s usually straightforward. If it’s structural, you’ll need a steel beam (RSJ—rolled steel joist) and Building Regulations approval.
How do I know if a wall is load-bearing?
Here are a few signs that a wall might be load-bearing:
- It feels solid (brick or block rather than stud and plasterboard).
- It’s located in the centre of the house, supporting joists or beams above.
- It runs perpendicular to floor joists.
- There’s another wall or beam directly above it on the upper floor.
- It aligns with beams or support structures in the loft or basement.
The only reliable way to be sure is to consult an experienced builder or structural engineer. They can assess the property’s structure and confirm what support is needed if you plan to remove it.
How Much Does It Cost To Remodel A House In 2025? A UK Guide
- Post author By ken
- Post date April 23, 2025
- No Comments on How Much Does It Cost To Remodel A House In 2025? A UK Guide
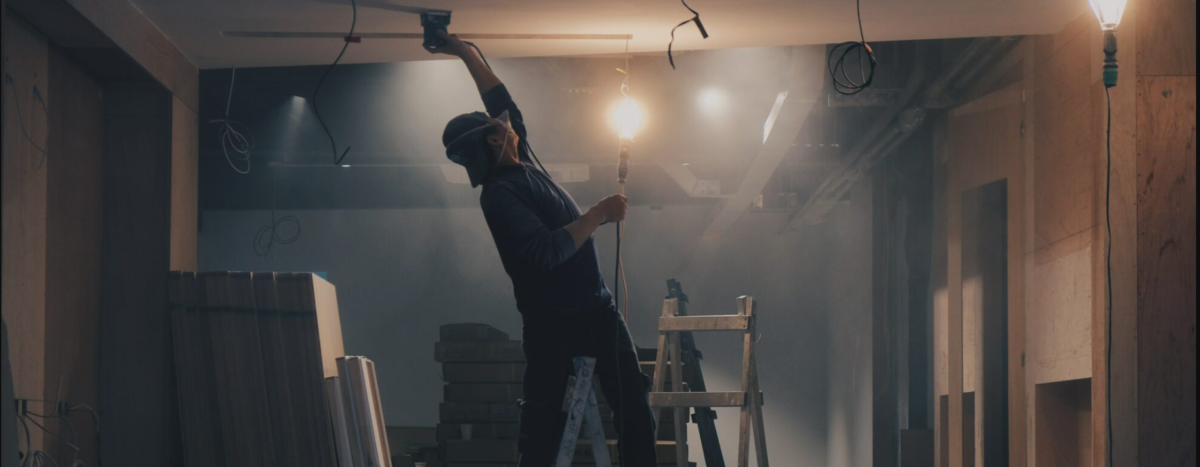
March 28th, 2025
When remodelling a house, costs can vary widely depending on the scope of work. The first thing to be mindful of is not to confuse remodelling with renovation. A renovation refreshes and restores existing rooms without altering their layout, whereas a remodel involves changing the internal structure—for example, removing walls to create an open-plan living, kitchen, and dining area.
Naturally, remodelling is more expensive. So, how much does it cost to remodel a house in 2025? In this article, we cover the costs of remodelling a 3-bedroom house (90m2 – the average size) comprising the following rooms:
- Kitchen-living-dining room
- Downstairs WC
- Boiler cupboard
- Cloakroom
- Entrance hall
- 3x bedrooms
- Bathroom
- En-suite
The calculations in this guide assume the existing shell remains, with no extensions.
We’ll take a look at the cost of remodelling a house by region, covering London, North England, Scotland, Wales, and Northern Ireland. We’ll also review average costs per square metre to help you budget accurately and avoid overspending.
Remodelling A House Cost Calculations
In terms of build specification, BuildPartner gives you three broad options to choose from:
- Basic spec is a basic finish; e.g., Leyland, Everest, Wickes.
- Standard spec is a standard finish; e.g., Dulux, Hamilton, Slim Line.
- Premium spec is a high-spec finish; e.g., Farrow & Ball, Fine Line, Siemens.
In this article, we’ve provided a breakdown of the cost of remodelling for all three specifications.
In addition to this, we have also provided three different benchmarks to show the range you can expect amongst different contractors. These are:
- Low benchmark – smaller companies are generally lower cost but less specialised and with low project management function; good for low/mid-spec projects and tight budgets.
- Mid benchmark – medium-sized companies offer a balanced mix of cost-effectiveness and specialisation; good for mid-range projects for effective execution within moderate budgets.
- High benchmark – larger companies generally have a higher cost base but can handle a wide variety of specialist tasks; good for mid/high-spec projects and project management.
Cost Of Remodelling A Three-Bed House (Basic Spec)
Below is a table showing the average cost of remodelling a three-bedroom house in the UK to a basic spec:
3-Bed Remodel (90m2) – Basic Spec | Total Average Build Cost | Average Cost Per Sq Metre | ||||
Low Benchmark | Mid Benchmark | High Benchmark | Low Benchmark | Mid Benchmark | High Benchmark | |
East Anglia | £118,891 | £132,941 | £145,911 | £1,321 | £1,477 | £1,621 |
Greater London | £127,609 | £143,967 | £157,890 | £1,418 | £1,600 | £1,754 |
Inner London | £130,838 | £146,508 | £154,460 | £1,454 | £1,628 | £1,716 |
Midlands | £114,363 | £127,878 | £140,354 | £1,271 | £1,421 | £1,559 |
North England | £112,356 | £125,635 | £137,892 | £1,248 | £1,396 | £1,532 |
Northern Ireland | £116,891 | £125,937 | £141,679 | £1,283 | £1,399 | £1,574 |
Scotland | £118,341 | £132,327 | £145,236 | £1,315 | £1,470 | £1,614 |
South East | £116,435 | £130,195 | £144,450 | £1,406 | £1,572 | £1,726 |
South West | £116,021 | £133,660 | £146,724 | £1,328 | £1,485 | £1,630 |
Wales | £112,488 | £125,782 | £135,727 | £1,250 | £1,398 | £1,508 |
Average | £118,423 | £132,483 | £145,032 | £1,329 | £1,485 | £1,624 |
All costs exclude VAT.
Here’s what the data shows for the cost of remodelling a three-bed house to a basic spec:
- It costs 9% more to remodel a house in Inner London than in other parts of the country.
- The minimum cost is £112,356, and the maximum cost is £157,890.
- The total average cost is £131,890, or £1,479 per square metre.
Start your free trial with BuildPartner to get a bespoke estimate of your construction project within minutes.
Cost Of Remodelling A Three-Bed House (Standard Spec)
Below is a table showing the average cost of remodelling a three-bedroom house to a standard spec:
3-Bed Remodel (90m2) – Mid Spec | Total Average Build Cost | Average Cost Per Sq Metre | ||||
Low Benchmark | Mid Benchmark | High Benchmark | Low Benchmark | Mid Benchmark | High Benchmark | |
East Anglia | £136,531 | £152,667 | £167,561 | £1,517 | £1,696 | £1,862 |
Greater London | £145,482 | £164,111 | £179,784 | £1,616 | £1,823 | £1,998 |
Inner London | £149,280 | £167,035 | £174,987 | £1,659 | £1,856 | £1,944 |
Midlands | £132,003 | £147,604 | £162,004 | £1,467 | £1,640 | £1,800 |
North England | £129,997 | £145,360 | £159,541 | £1,444 | £1,615 | £1,773 |
Northern Ireland | £134,532 | £145,181 | £163,328 | £1,479 | £1,613 | £1,815 |
Scotland | £135,981 | £152,052 | £166,886 | £1,511 | £1,689 | £1,854 |
South East | £132,664 | £148,342 | £162,815 | £1,602 | £1,792 | £1,966 |
South West | £133,661 | £153,386 | £168,374 | £1,524 | £1,704 | £1,871 |
Wales | £130,129 | £145,508 | £156,575 | £1,446 | £1,617 | £1,740 |
Average | £136,026 | £152,124 | £166,186 | £1,527 | £1,705 | £1,862 |
All costs exclude VAT.
Here’s what the data shows for the cost of remodelling a three-bed house to a standard spec:
- The minimum cost is £129,997, and the maximum cost is £179,784.
- The total average cost is £151,445, or £1,698 per square metre.
Cost Of Remodelling A Three-Bed House (Premium Spec)
Below is a table showing the average cost of remodelling a three-bedroom house to a premium spec:
3-Bed Remodel (90m2) – Premium Spec | Total Average Build Cost | Average Cost Per Sq Metre | ||||
Low Benchmark | Mid Benchmark | High Benchmark | Low Benchmark | Mid Benchmark | High Benchmark | |
East Anglia | £168,958 | £188,926 | £207,358 | £1,877 | £2,099 | £2,304 |
Greater London | £177,677 | £201,196 | £219,336 | £1,974 | £2,236 | £2,437 |
Inner London | £183,181 | £204,768 | £212,720 | £2,035 | £2,275 | £2,364 |
Midlands | £164,430 | £183,863 | £201,801 | £1,827 | £2,043 | £2,242 |
North England | £162,424 | £181,619 | £199,338 | £1,805 | £2,018 | £2,215 |
Northern Ireland | £159,175 | £177,987 | £195,351 | £1,769 | £1,978 | £2,171 |
Scotland | £168,408 | £188,311 | £206,683 | £1,871 | £2,092 | £2,296 |
South East | £162,497 | £181,701 | £201,595 | £1,806 | £2,019 | £2,240 |
South West | £166,088 | £189,645 | £208,170 | £1,845 | £2,107 | £2,313 |
Wales | £162,556 | £181,767 | £194,897 | £1,806 | £2,020 | £2,166 |
Average | £167,539 | £187,978 | £204,725 | £1,862 | £2,089 | £2,275 |
All costs exclude VAT.
Here’s what the data shows for the cost of remodelling a three-bed house to a premium spec:
- The minimum cost is £159,175, and the maximum cost is £219,336.
- The total average cost is £186,747, or £2,075 per square metre.
Summary Of The Average Cost To Remodel A House
So, how much does it cost to remodel a house in the UK? Based on the three specifications covered in this article, you can expect remodelling a house to cost on average (when using a mid-benchmark contractor):
- Basic spec: £132,483, or £1,485 per square metre.
- Standard spec: £152,124, or £1,705 per square metre.
- Premium spec: £187,978, or £2,089 per square metre.
The costs in this guide exclude extensions. If you’re planning to build an extension, you should factor in approximately £2,900 per square metre for a ground-floor extension, and £2,400 for a double-storey rear extension. For more specific information about extension costs, check out this article.
Please remember that all costs exclude VAT.
Start your free trial with BuildPartner to get a bespoke estimate of your construction project within minutes.
Frequently Asked Questions About Remodelling A House
Here are some frequently asked questions about remodelling a house.
How long does it take to remodel a house?
Remodelling a three-bed house takes an average of 20.9 weeks with an average of two tradespeople carrying out the work. Here’s a rough breakdown of the project:
- Demolitions take place early, lasting about five weeks.
- External and internal wall structures are built simultaneously.
- Windows and doors are installed, followed by internal doors and frames.
- Drainage and pipework progress alongside heating and cooling system installations.
- Electrical work, including wiring, fuse boards, and appliances, occurs mid-project.
- Ceiling and wall preparation, flooring, and kitchen installations follow.
- Joinery, decoration, and fixtures and fittings finalise the remodel in the last weeks.
As ever, progress heavily depends on the alignment of tradesmen at key stages. For instance, delays in external and internal wall construction in weeks 5–7 can push back heating and electrical work scheduled for the following weeks.
What is the difference between remodelling and renovating a house?
Remodelling and renovating are often used interchangeably, but they’re not the same. Renovating involves restoring or updating existing features, whereas remodelling alters the structure or floor plan—for example, removing walls to create an open-plan living, kitchen, and dining area.
Should I move out when remodelling a house?
It’s a good idea to move out during a home remodel, especially for larger projects. The disruption from contractors needing access at awkward times, the dust and debris, and the noise make for uncomfortable living. Additionally, at certain times, you’ll need to switch off the electricity to carry out work, which will leave you without power (and wi-fi!).
If plumbers are working, you’ll have no access to washing, cooking, or heating, which can be particularly challenging during the winter. Then, there are also safety concerns with power tools and other hazards being left out, especially if you have young children. It’s better to find alternative accommodation.
How Much Does It Cost To Build A Bungalow In 2025? A UK Guide
- Post author By ken
- Post date April 23, 2025
- No Comments on How Much Does It Cost To Build A Bungalow In 2025? A UK Guide
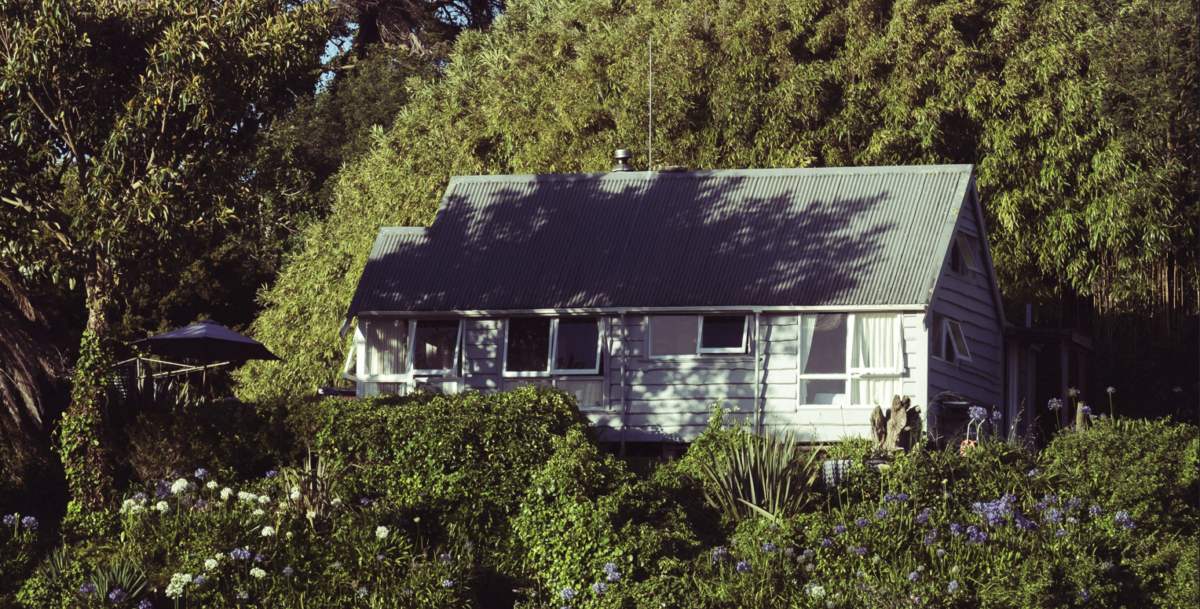
March 28th, 2025
There is a distinct shortage of bungalows in the UK, and the average price has tripled in the last 25 years, which is further exacerbated by a lack of new builds. In 1996, for example, 7% of new-build properties were bungalows, according to the National House Building Council; today, that figure has slowed to just 1%.
That drop can be largely attributed due to a shift in planning policy—there is a much greater focus on sustainability by making the best use of sites and reducing footprint (often through building larger dwellings and more storeys). However, while many developers focus on large-scale projects, building a bungalow remains an attractive option for self-builders or individual projects.
So, how much does it cost to build a bungalow?
Naturally, building costs vary by size, type, and complexity, so in this article, we’ll cover the cost of building a bungalow across various regions in the UK.
To give you an accurate view, we’ll compare the cost of building three different types of bungalows:
- Two-bedroom bungalow (90m2)
- Three-bedroom bungalow (100m2)
- Three-bedroom bungalow with garage and driveway (125m2)
We’ll delve into the cost breakdown for each bungalow by region. We’ll also review the average costs per sq metre, to ensure your project is accurately costed and to minimise overspend.
How Bungalow Construction Has Evolved In The UK
Historically, bungalows in the UK were often built as affordable homes using simple timber frame construction and trussed rafter roofs. This allowed for quick, low-cost builds.
However, with bungalows now in high demand—especially among downsizers and those seeking future-proof homes—developers are turning to more robust materials and modern construction techniques, such as insulated concrete formwork (ICF), structural insulated panels (SIPs), or high-spec masonry builds.
These methods improve energy efficiency, longevity, and design flexibility, but they can also push up the cost per square metre, meaning today’s bungalows are often anything but cheap.
Building A Bungalow Construction Cost Calculations
In terms of build specification, BuildPartner gives you three broad options to choose from:
- Low spec is a basic finish; e.g., Leyland, Everest, Wickes.
- Standard spec is a standard finish; e.g., Dulux, Hamilton, Slim Line.
- Premium spec is a high-spec finish; e.g., Farrow & Ball, Fine Line, Siemens.
To keep this comparison simple, we have chosen standard spec in all our cost estimations. In addition to this, we have also provided three different benchmarks to show the range you can expect amongst different contractors. These are:
- Low benchmark – smaller companies are generally lower cost but less specialised and with low project management function; good for low/mid-spec projects and tight budgets.
- Mid benchmark – medium-sized companies offer a balanced mix of cost-effectiveness and specialisation; good for mid-range projects for effective execution within moderate budgets.
- High benchmark – larger companies generally have a higher cost base but can handle a wide variety of specialist tasks; good for mid/high-spec projects and project management.
Cost Of Building A Two-Bed Bungalow (90m2)
Below is a table showing the average cost of building a two-bedroom bungalow (90m2) in the UK, comprising the following rooms:
- Two bedrooms
- Lounge
- Kitchen-diner
- Bathroom
- Cloakroom
- Pantry
Two-bed bungalow (90m2) | Total Average Build Cost | Average Cost Per Sq Metre | ||||
Low Benchmark | Mid Benchmark | High Benchmark | Low Benchmark | Mid Benchmark | High Benchmark | |
East Anglia | £167,924 | £187,769 | £206,088 | £1,866 | £2,086 | £2,290 |
Greater London | £179,420 | £201,153 | £223,788 | £1,994 | £2,235 | £2,487 |
Inner London | £183,517 | £204,999 | £213,678 | £2,039 | £2,278 | £2,374 |
Midlands | £163,372 | £182,679 | £200,502 | £1,815 | £2,030 | £2,228 |
North England | £160,384 | £179,338 | £196,834 | £1,782 | £1,993 | £2,187 |
Northern Ireland | £165,666 | £179,736 | £202,203 | £1,831 | £1,997 | £2,247 |
Scotland | £166,574 | £186,261 | £204,433 | £1,851 | £2,070 | £2,271 |
South East | £162,780 | £182,017 | £201,946 | £1,966 | £2,198 | £2,413 |
South West | £164,992 | £189,182 | £207,678 | £1,880 | £2,102 | £2,308 |
Wales | £160,764 | £179,764 | £192,907 | £1,786 | £1,997 | £2,143 |
Average | £167,539 | £187,290 | £205,006 | £1,881 | £2,099 | £2,295 |
All costs exclude VAT.
Here’s what the data shows for the cost of building a two-bed bungalow (90m2):
- It costs 8% more to build a bungalow in Inner London than in other parts of the country.
- The minimum cost is £160,384, and the maximum cost is £223,788.
- The total average cost is £186,612, or £2,091 per square metre.
Start your free trial with BuildPartner today to get the most accurate estimate of your construction project.
Cost Of Building A Three-Bed Bungalow (100m2)
Below is a table showing the average cost of building a three-bedroom bungalow (100m2) in the UK, comprising the following rooms:
-
- Three bedrooms
- Lounge
- Kitchen-diner
- Bathroom
- Cloakroom
- Pantry
- Separate WC
Three-bed bungalow (100m2) | Total Average Build Cost | Average Cost Per Sq Metre | ||||
Low Benchmark | Mid Benchmark | High Benchmark | Low Benchmark | Mid Benchmark | High Benchmark | |
East Anglia | £173,880 | £194,429 | £213,398 | £1,739 | £1,944 | £2,134 |
Greater London | £185,807 | £208,312 | £231,980 | £1,858 | £2,083 | £2,320 |
Inner London | £190,091 | £212,335 | £221,406 | £1,901 | £2,123 | £2,214 |
Midlands | £169,139 | £189,128 | £207,580 | £1,691 | £1,891 | £2,076 |
North England | £166,059 | £185,684 | £203,799 | £1,661 | £1,857 | £2,038 |
Northern Ireland | £171,525 | £186,071 | £209,329 | £1,706 | £1,861 | £2,093 |
Scotland | £172,484 | £192,869 | £211,686 | £1,725 | £1,929 | £2,117 |
South East | £168,621 | £188,548 | £206,943 | £1,833 | £2,049 | £2,249 |
South West | £170,846 | £195,891 | £215,044 | £1,752 | £1,959 | £2,150 |
Wales | £166,470 | £186,144 | £199,780 | £1,665 | £1,861 | £1,998 |
Average | £173,492 | £193,941 | £212,094 | £1,753 | £1,956 | £2,139 |
All costs exclude VAT.
Here’s what the data shows for the cost of building a three-bed bungalow:
- The minimum cost is £166,059, and the maximum cost is £231,980.
- The total average cost is £193,176, or £1,949 per square metre.
Cost Of Building A Three-Bed Bungalow With Garage & Driveway (125m2)
Below is a table showing the average cost of building a three-bedroom bungalow (125m2) with a garage and driveway, comprising the following rooms:
- Three bedrooms
- Lounge
- Kitchen-diner
- Bathroom
- Cloakroom
- Pantry
- Separate WC
- Garage with a pitched roof
- Driveway
Three-bed bungalow w. garage/driveway (125m2) | Total Average Build Cost | Average Cost Per Sq Metre | ||||
Low Benchmark | Mid Benchmark | High Benchmark | Low Benchmark | Mid Benchmark | High Benchmark | |
East Anglia | £210,536 | £235,418 | £258,386 | £1,684 | £1,883 | £2,067 |
Greater London | £224,699 | £252,438 | £279,803 | £1,798 | £2,020 | £2,238 |
Inner London | £229,538 | £257,061 | £267,309 | £1,836 | £2,056 | £2,138 |
Midlands | £204,775 | £228,976 | £251,315 | £1,638 | £1,832 | £2,011 |
North England | £200,723 | £224,445 | £246,342 | £1,606 | £1,796 | £1,971 |
Northern Ireland | £196,708 | £219,956 | £241,415 | £1,574 | £1,760 | £1,931 |
Scotland | £207,615 | £232,152 | £254,801 | £1,661 | £1,857 | £2,038 |
South East | £203,831 | £227,920 | £252,875 | £1,631 | £1,823 | £2,023 |
South West | £206,747 | £237,528 | £260,748 | £1,654 | £1,900 | £2,086 |
Wales | £201,032 | £224,790 | £241,241 | £1,608 | £1,798 | £1,930 |
Average | £208,621 | £234,068 | £255,424 | £1,669 | £1,873 | £2,043 |
All costs exclude VAT.
Here’s what the data shows for the cost of building a three-bed bungalow with a garage and driveway (125m2):
- The minimum cost is £196,708, and the maximum cost is £279,803.
- The total average cost is £232,704, or £1,862 per square metre.
Summary Of The Average Cost To Build A Bungalow
So, how much does it cost to build a bungalow in the UK? That depends largely on where you are building. If you’re building a bungalow in London, it will cost you an average of 13% more.
Based on the three types of bungalows covered in this article, you can expect building a bungalow to cost on average (when using a mid-benchmark contractor):
- Two-bed bungalow (90m2) – £187,290, or £2,099 per square metre.
- Three-bed bungalow (100m2) – £193,941, or £1,956 per square metre.
- Three-bed bungalow w. garage/driveway (125m2) – £234,068, or £1,873 per square metre.
Please remember that all costs exclude VAT.
Start your free trial with BuildPartner to get an accurate estimate of your construction project within minutes.
Frequently Asked Questions About Building A Bungalow
Here are some frequently asked questions about building a bungalow.
How long does it take to build a bungalow?
Building a three-bed bungalow (with a garage) takes an average of 26.85 weeks with an average of two tradespeople carrying out the work. The process begins with preliminaries, demolitions, and foundation work in the first six weeks, followed by the construction of structural elements, including steel supports, external walls, and roofing, which continues until approximately week 10.
By weeks 9 to 16, windows, doors, drainage, heating, and electrical systems are installed. In the final stages, from weeks 16 to 27, work on joinery, decoration, fixtures, and external elements takes place.
What is the ideal size for a bungalow?
A typical two-bedroom bungalow is around 60–80m², while a three-bedroom design ranges from 90–120m². Adding a single garage typically increases the size by 15–20m², while a double garage adds approximately 30–40m², providing enough space for two cars and extra storage.
Do bungalows hold their value?
Demand to downsize is increasing, and many bungalows that are put on the market are snapped up quickly. Regency Living found that bungalows currently account for just one in 10 homes listed for sale. Regional data shows the varying availability of bungalows:
- London: 2%
- South West: 13%
- Yorkshire: 12%
Despite their relatively small share of the housing market, the demand for bungalows remains high. The average price soared for three consecutive years but declined slightly in the most recent calendar year, as reported by Statista, and since the year 2000, bungalow prices have tripled.
How Much Does It Cost To Build A Porch In 2025? A UK Guide
- Post author By ken
- Post date March 24, 2025
- No Comments on How Much Does It Cost To Build A Porch In 2025? A UK Guide
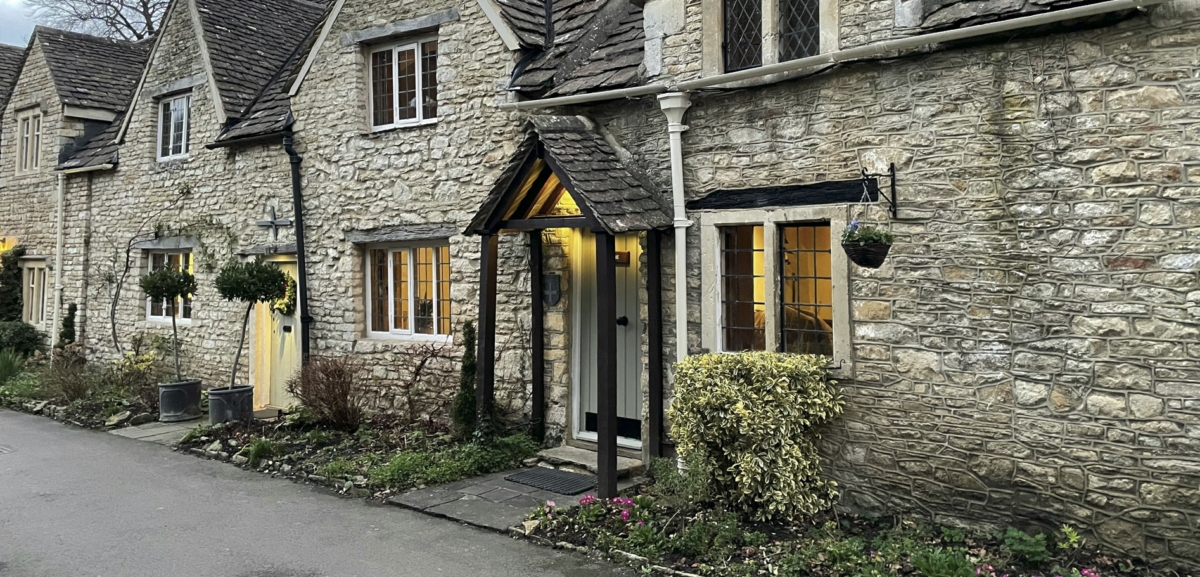
February 28th, 2025
Building a porch is a great way to enhance your home’s kerb appeal, add extra storage, and improve insulation (heat loss through windows and doors accounts for 20–30% of the whole heat loss of house). A porch also improves home security by adding an extra layer of protection.
But costs can vary widely depending on size, materials, and whether the structure is enclosed or open. In this guide, we’ll break down the key factors affecting porch costs in the UK, comparing four different types of porches:
- Brick porch – constructed with bricks.
- Rendered porch – built with blocks and a rendered finish.
- Timber porch (enclosed) – made primarily from wood.
- Open porch – without enclosed walls, and offering an external shelter.
Here's a breakdown of the costs for different types of porches, so you can determine which option best suits your project.
Building A Porch Construction Cost Calculations
Our cost comparisons are based on a gross external floor area (GEFA) of 3m². The only exception is the open porch, which is based on a GEFA of 2m2. Since an open porch is primarily an aesthetic shelter, a smaller size better reflects its typical usage.
In terms of build specification BuildPartner pricing tool gives you three broad options (which can be revised by item at a later point):
- Low spec is a basic finish; e.g. Leyland, Everest, Wickes.
- Mid spec is a standard finish; e.g. Dulux, Hamilton, Slim Line.
- High spec is a high-spec finish; e.g. Farrow & Ball, Fine Line, Siemens.
To keep this comparison simple, we have chosen mid spec in all our cost estimations. In addition to this, we have also provided three different benchmarks to show the range you can expect amongst different contractors. These are:
- Low benchmark – smaller companies are generally lower cost but less specialised and with low project management function; good for low/mid-spec projects and tight budgets.
- Mid benchmark – medium-sized companies offer a balanced mix of cost-effectiveness and specialisation; good for mid-range projects for effective execution within moderate budgets.
- High benchmark – larger companies generally have a higher cost base but can handle a wide variety of specialist tasks; good for mid/high-spec projects and project management.
Cost Of Building A Brick Porch
Here’s a table showing the average cost of building a 3m2 brick porch in the UK:
Brick Porch | Total Average Build Cost | Average Cost Per Sq Metre | ||||
Low Benchmark | Mid Benchmark | High Benchmark | Low Benchmark | Mid Benchmark | High Benchmark | |
East Anglia | £7,582 | £8,276 | £8,961 | £2,527 | £2,759 | £2,987 |
Greater London | £8,170 | £9,427 | £9,553 | £2,723 | £3,142 | £3,184 |
Inner London | £8,176 | £9,275 | £9,988 | £2,725 | £3,092 | £3,329 |
Midlands | £7,377 | £8,048 | £8,719 | £2,459 | £2,683 | £2,906 |
North England | £7,182 | £7,857 | £8,488 | £2,394 | £2,619 | £2,829 |
Northern Ireland | £7,465 | £8,179 | £8,860 | £2,499 | £2,726 | £2,953 |
Scotland | £7,432 | £8,108 | £8,784 | £2,477 | £2,703 | £2,928 |
South East | £7,284 | £8,145 | £9,037 | £2,639 | £2,951 | £3,239 |
South West | £7,421 | £8,560 | £9,395 | £2,552 | £2,853 | £3,132 |
Wales | £7,187 | £8,036 | £8,616 | £2,396 | £2,679 | £2,872 |
Average | £7,528 | £8,391 | £9,040 | £2,539 | £2,821 | £3,036 |
All costs exclude VAT.
Here’s what the data shows for the cost of building a brick porch:
- It costs 13% more to build a porch in London than in other regions.
- The minimum cost is £7,182, and the maximum cost is £9,988.
- The total average cost is £8,320, or £2,799 per square metre.
Start your free trial with BuildPartner today to get the most accurate estimate of your construction project.
Cost Of Building A Timber Porch
Here’s a table showing the average cost of building a 3m2 timber porch in the UK:
Timber Porch (Enclosed) | Total Average Build Cost | Average Cost Per Sq Metre | ||||
Low Benchmark | Mid Benchmark | High Benchmark | Low Benchmark | Mid Benchmark | High Benchmark | |
East Anglia | £6,268 | £6,842 | £7,407 | £2,089 | £2,281 | £2,469 |
Greater London | £6,702 | £7,609 | £8,042 | £2,234 | £2,536 | £2,681 |
Inner London | £6,812 | £7,653 | £8,319 | £2,271 | £2,551 | £2,773 |
Midlands | £6,140 | £6,698 | £7,257 | £2,047 | £2,233 | £2,419 |
North England | £6,038 | £6,588 | £7,136 | £2,013 | £2,196 | £2,379 |
Northern Ireland | £6,233 | £6,773 | £7,338 | £2,070 | £2,258 | £2,446 |
Scotland | £6,257 | £6,825 | £7,394 | £2,086 | £2,275 | £2,465 |
South East | £6,037 | £6,750 | £7,409 | £2,187 | £2,446 | £2,684 |
South West | £6,171 | £7,069 | £7,759 | £2,107 | £2,356 | £2,586 |
Wales | £6,019 | £6,730 | £7,206 | £2,006 | £2,243 | £2,402 |
Average | £6,268 | £6,954 | £7,527 | £2,111 | £2,338 | £2,530 |
All costs exclude VAT.
Here’s what the data shows for the cost of building a timber porch:
- The minimum cost is £6,019, and the maximum cost is £8,319.
- The total average cost is £6,916, or £2,326 per square metre.
Cost Of Building A Rendered Porch
Here’s a table showing the average cost of building a 3m2 rendered porch in the UK:
Rendered Porch | Total Average Build Cost | Average Cost Per Sq Metre | ||||
Low Benchmark | Mid Benchmark | High Benchmark | Low Benchmark | Mid Benchmark | High Benchmark | |
East Anglia | £5,298 | £5,784 | £6,261 | £1,766 | £1,928 | £2,087 |
Greater London | £5,747 | £6,428 | £6,713 | £1,916 | £2,143 | £2,238 |
Inner London | £5,738 | £6,465 | £7,010 | £1,913 | £2,155 | £2,337 |
Midlands | £5,160 | £5,629 | £6,098 | £1,720 | £1,876 | £2,033 |
North England | £5,025 | £5,494 | £5,938 | £1,675 | £1,831 | £1,979 |
Northern Ireland | £4,924 | £5,384 | £5,820 | £1,641 | £1,795 | £1,940 |
Scotland | £5,209 | £5,683 | £6,157 | £1,736 | £1,894 | £2,052 |
South East | £5,111 | £5,715 | £6,341 | £1,704 | £1,905 | £2,114 |
South West | £5,185 | £5,975 | £6,558 | £1,728 | £1,992 | £2,186 |
Wales | £5,027 | £5,621 | £6,030 | £1,676 | £1,874 | £2,010 |
Average | £5,242 | £5,818 | £6,293 | £1,747 | £1,939 | £2,098 |
All costs exclude VAT.
Here’s what the data shows for the cost of building a rendered porch:
- The minimum cost is £4,924, and the maximum cost is £7,010.
- The total average cost is £5,784, or £1,928 per square metre.
Cost Of Building An Open Porch
Here’s a table showing the average cost of building a 2m2 open porch:
Open Porch | Total Average Build Cost | Average Cost Per Sq Metre | ||||
Low Benchmark | Mid Benchmark | High Benchmark | Low Benchmark | Mid Benchmark | High Benchmark | |
East Anglia | £3,439 | £3,751 | £4,064 | £1,719 | £1,876 | £2,032 |
Greater London | £3,741 | £4,254 | £4,344 | £1,871 | £2,127 | £2,172 |
Inner London | £3,755 | £4,312 | £4,552 | £1,877 | £2,156 | £2,276 |
Midlands | £3,325 | £3,628 | £3,930 | £1,663 | £1,814 | £1,965 |
North England | £3,254 | £3,550 | £3,846 | £1,627 | £1,775 | £1,923 |
Northern Ireland | £3,358 | £3,705 | £4,013 | £1,698 | £1,852 | £2,007 |
Scotland | £3,321 | £3,623 | £3,924 | £1,660 | £1,811 | £1,962 |
South East | £3,327 | £3,721 | £4,128 | £1,808 | £2,022 | £2,219 |
South West | £3,367 | £3,918 | £4,301 | £1,752 | £1,959 | £2,150 |
Wales | £3,295 | £3,612 | £3,880 | £1,615 | £1,806 | £1,940 |
Average | £3,418 | £3,807 | £4,098 | £1,729 | £1,920 | £2,065 |
All costs exclude VAT.
Here’s what the data shows for the cost of building an open porch:
- The minimum cost is £3,254, and the maximum cost is £4,552.
- The total average cost is £3,755, or £1,905 per square metre.
Summary Of The Average Cost To Build A Porch
So, how much does it cost to build a new porch in the UK? That depends largely on where you are building. If you’re building a porch in London, it will cost you an average of 13% more.
Based on the four different types of porches covered in this article, you can expect building a porch to cost on average (when using a mid-benchmark contractor):
- Brick porch – £8,391, or £2,821 per square metre
- Timber porch – £6,954, or £2,338 per square metre
- Rendered porch – £5,818, or £1,939 per square metre
- Open porch – £3,807, or £1,920 per square metre
Please remember that all costs exclude VAT.
Start your free trial with BuildPartner today to get the most accurate estimate of your construction project.
Frequently Asked Questions About Building A Porch
Here are some frequently asked questions about building a porch.
Can a porch prevent heat loss in my home?
Building a porch improves energy efficiency by creating an air buffer that traps cold air before it reaches your main entrance. It also acts as a thermal barrier, providing an additional layer of protection against the elements.
The most energy-efficient porches are made from brick and timber, which benefit from greater thermal mass to regulate temperature. uPVC is less efficient without high-quality glazing and seals.
Does adding a porch increase security and reduce the risk of burglary?
If you keep your existing front door, the porch effectively provides double security—a potential intruder would have to get past both the porch and your door to gain entry. This added barrier can significantly deter burglars.
Is a porch good for storage?
A porch is great for storage because it can act as a cloakroom or boot room, providing space for coats, boots, bags, and outdoor gear. No more coats draped over chairs or shoes scattered around the hallway—it's a purposeful space for your outdoor items.
What are the downsides of getting a uPVC porch?
uPVC porches are generally less energy-efficient and can allow more heat to escape. Additionally, while uPVC porches can last 20 to 30 years, they can become brittle, yellow, or fade with age, especially when exposed to harsh weather conditions. They aren’t as visually appealing as natural materials like brick or timber.
How Much Does It Cost To Build A Garage In 2025? A UK Guide
- Post author By ken
- Post date March 20, 2025
- No Comments on How Much Does It Cost To Build A Garage In 2025? A UK Guide
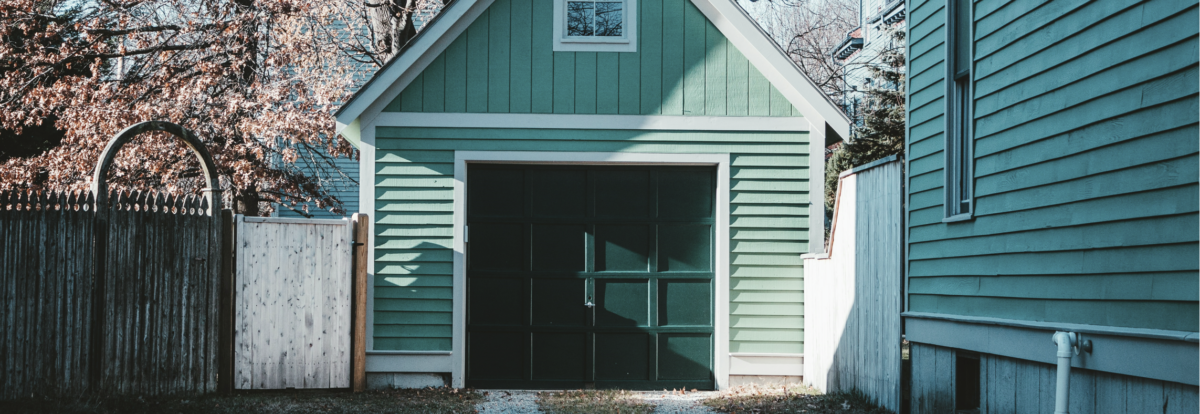
The cost of building a garage continues to be influenced by rising material prices, labour rates, and regional variations across the UK. Whether you’re looking to build a small single garage or a spacious double garage, understanding the costs involved is essential to avoid cost overruns.
In this guide, we’ll provide a detailed comparison of four popular garage types: single garage with a flat roof, single garage with a pitched roof, double garage with a flat roof, and double garage with a pitched roof. This guide also includes regional rate comparisons across the UK, along with building costs per square metre.
Building A Garage Construction Cost Calculations
In our calculations, we applied a consistent methodology across different regions. The cost comparisons assume the garage is an extension to an existing dwelling, not a new detached structure. These cost excludes the installation of appliances and EV chargers.
The typical sizes of garages in the UK are:
- Single – 10 x 18 feet (3m × 5.5m, with a gross external area of 16.5m2)
- Double – 18 x 18 feet (5.5m × 6m, with a gross external area of 33m2)
We have used both of these measurements to calculate the costs in this article.
In terms of build specification when using our BuildPartner pricing tool, our pricing calculator gives you three broad options (which can be revised by item at a later point):
- Low spec is a basic finish; e.g. Leyland, Everest, Wickes.
- Standard spec is a standard finish; e.g. Dulux, Hamilton, Slim Line.
- Premium spec is a high-spec finish; e.g. Farrow & Ball, Fine Line, Siemens.
To keep this comparison simple, we have chosen standard spec in all our cost estimations.
In addition to this, we have also provided three different benchmarks to show the range you can expect amongst different contractors. These are:
- Low benchmark – smaller companies are generally lower cost but less specialised and with low project management function; good for low/mid-spec projects and tight budgets.
- Mid benchmark – medium-sized companies offer a balanced mix of cost-effectiveness and specialisation; good for mid-range projects for effective execution within moderate budgets.
- High benchmark – larger companies generally have a higher cost base but can handle a wide variety of specialist tasks; good for mid/high-spec projects and project management.
In short, contractor pricing varies due to factors such as expertise, location, and project intricacies.
How Much Does It Cost To Build A Single Garage With A Flat Roof?
Here’s a table showing the average building costs of a single garage with a flat roof for a standard-spec project in the UK:
Single Garage With Flat Roof | Total Average Build Cost | Average Cost Per Sq Metre | ||||
Low Benchmark | Mid Benchmark | High Benchmark | Low Benchmark | Mid Benchmark | High Benchmark | |
East Anglia | £34,642 | £37,791 | £40,941 | £2,100 | £2,290 | £2,481 |
Greater London | £36,188 | £40,465 | £45,089 | £2,193 | £2,452 | £2,733 |
Inner London | £37,152 | £41,431 | £45,381 | £2,252 | £2,511 | £2,750 |
Midlands | £33,738 | £36,805 | £39,872 | £2,045 | £2,231 | £2,416 |
North England | £32,837 | £35,822 | £38,808 | £1,990 | £2,171 | £2,352 |
Northern Ireland | £33,418 | £36,522 | £39,566 | £2,029 | £2,213 | £2,398 |
Scotland | £33,357 | £36,390 | £39,422 | £2,022 | £2,205 | £2,389 |
South East | £36,025 | £40,282 | £44,212 | £2,183 | £2,441 | £2,680 |
South West | £33,961 | £39,293 | £43,126 | £2,130 | £2,381 | £2,614 |
Wales | £32,782 | £36,656 | £39,285 | £1,987 | £2,222 | £2,381 |
Average | £34,410 | £38,146 | £41,570 | £2,093 | £2,312 | £2,519 |
All costs exclude VAT.
Here’s what the data shows for the cost of building a single garage with a flat roof:
- It costs 11% more to build a garage in London than in other regions.
- The minimum cost is £32,782, and the maximum cost is £45,381.
- The total average cost is £38,042, or £2,308 per square metre.
How Much Does It Cost To Build A Single Garage With A Pitched Roof?
Here’s a table showing the average building costs of a single garage with a pitched roof for a standard-spec project in the UK:
Single Garage With Pitched Roof | Total Average Build Cost | Average Cost Per Sq Metre | ||||
Low Benchmark | Mid Benchmark | High Benchmark | Low Benchmark | Mid Benchmark | High Benchmark | |
East Anglia | £41,399 | £45,163 | £48,927 | £2,509 | £2,737 | £2,965 |
Greater London | £43,858 | £49,041 | £54,502 | £2,658 | £2,972 | £3,303 |
Inner London | £44,837 | £50,017 | £54,799 | £2,717 | £3,031 | £3,321 |
Midlands | £40,239 | £43,898 | £47,556 | £2,439 | £2,660 | £2,882 |
North England | £39,233 | £42,800 | £46,367 | £2,378 | £2,594 | £2,810 |
Northern Ireland | £39,568 | £43,082 | £46,673 | £2,393 | £2,611 | £2,829 |
Scotland | £39,644 | £43,248 | £46,851 | £2,403 | £2,621 | £2,839 |
South East | £43,495 | £48,635 | £53,380 | £2,636 | £2,948 | £3,235 |
South West | £40,587 | £47,114 | £51,711 | £2,554 | £2,855 | £3,134 |
Wales | £39,040 | £43,654 | £46,910 | £2,366 | £2,646 | £2,843 |
Average | £41,190 | £45,665 | £49,767 | £2,505 | £2,768 | £3,016 |
All costs exclude VAT.
Here’s what the data shows for the cost of building a single garage with a pitched roof:
- The minimum cost is £39,040, and the maximum cost is £54,799.
- The total average cost is £45,451, or £2,763 per square metre.
How Much Does It Cost To Build A Double Garage With A Flat Roof?
Here’s a table showing the average building costs of a double garage with a flat roof for a standard-spec project in the UK:
Double Garage With Flat Roof | Total Average Build Cost | Average Cost Per Sq Metre | ||||
Low Benchmark | Mid Benchmark | High Benchmark | Low Benchmark | Mid Benchmark | High Benchmark | |
East Anglia | £47,969 | £52,330 | £56,690 | £1,454 | £1,586 | £1,718 |
Greater London | £48,484 | £54,214 | £60,139 | £1,469 | £1,643 | £1,822 |
Inner London | £50,304 | £56,249 | £62,413 | £1,524 | £1,705 | £1,891 |
Midlands | £46,603 | £50,839 | £55,076 | £1,412 | £1,541 | £1,669 |
North England | £45,307 | £49,426 | £53,544 | £1,373 | £1,498 | £1,623 |
Northern Ireland | £46,036 | £50,338 | £54,533 | £1,395 | £1,525 | £1,653 |
Scotland | £45,930 | £50,105 | £54,280 | £1,392 | £1,518 | £1,645 |
South East | £50,094 | £56,014 | £61,479 | £1,518 | £1,697 | £1,863 |
South West | £46,968 | £54,549 | £59,871 | £1,423 | £1,653 | £1,814 |
Wales | £45,153 | £50,489 | £54,183 | £1,368 | £1,530 | £1,642 |
Average | £47,285 | £52,455 | £57,221 | £1,433 | £1,590 | £1,734 |
All costs exclude VAT.
Here’s what the data shows for the cost of building a double garage with a flat roof:
- The minimum cost is £45,153, and the maximum cost is £62,413.
- The total average cost is £52,530, or £1,585 per square metre.
How Much Does It Cost To Build A Double Garage With A Pitched Roof?
Here’s a table showing the average building costs of a double garage with a pitched roof for a standard-spec project in the UK:
Double Garage With Pitched Roof | Total Average Build Cost | Average Cost Per Sq Metre | ||||
Low Benchmark | Mid Benchmark | High Benchmark | Low Benchmark | Mid Benchmark | High Benchmark | |
East Anglia | £58,327 | £63,630 | £68,932 | £1,767 | £1,928 | £2,089 |
Greater London | £62,074 | £69,410 | £76,858 | £1,881 | £2,103 | £2,329 |
Inner London | £63,422 | £70,761 | £77,536 | £1,922 | £2,144 | £2,350 |
Midlands | £56,574 | £61,717 | £66,860 | £1,714 | £1,870 | £2,026 |
North England | £55,123 | £60,135 | £65,146 | £1,670 | £1,822 | £1,974 |
Northern Ireland | £55,523 | £60,456 | £65,494 | £1,679 | £1,832 | £1,985 |
Scotland | £55,628 | £60,685 | £65,742 | £1,686 | £1,839 | £1,992 |
South East | £61,551 | £68,825 | £75,540 | £1,865 | £2,086 | £2,289 |
South West | £57,132 | £66,529 | £73,020 | £1,803 | £2,016 | £2,213 |
Wales | £54,766 | £61,238 | £65,894 | £1,660 | £1,856 | £1,997 |
Average | £58,012 | £64,339 | £70,102 | £1,765 | £1,950 | £2,124 |
All costs exclude VAT.
Here’s what the data shows for the cost of building a single garage with a pitched roof:
- The minimum cost is £54,766, and the maximum cost is £77,536.
- The total average cost is £64,151, or £1,964 per square metre.
How Long Does It Take To Build A Garage?
Based on a typical timeline, it would take approximately 4.5 weeks to build a garage with an average of two tradespeople, with an estimated breakdown by project stage of:
- Demolitions: 0.5 days
- Foundations and substructure: 6.5 days
- Steel and structural supports: 0.2 days
- External wall structure and lining: 9.1 days
- Roof structure and coverings: 1.4 days
- External windows and doors: 1.5 days
- Drainage and pipework: 1 day
- Wiring and fuseboards: 0.3 days
- Wired appliances: 0.5 days
- Ceiling preparation and finishes: 0.5 days
- Wall preparation and finishes: 1.2 days
Summary Of The Average Cost To Build A Garage
So, how much does it cost to build a new garage in the UK? That depends largely on where you are building. If you’re building a garage in London, it will cost you an average of 11% more. Based on the four different types of garages covered in this article, you can expect building a garage to cost on average (when using a mid-benchmark contractor):
- Single with flat roof – £38,146, or £2,312 per square metre
- Single with pitched roof – £45,655, or £2,768 per square metre
- Double with flat roof – £52,455, or £1,590 per square metre
- Double with pitched roof – £64,339, or £1,950 per square metre
Please remember that all costs exclude VAT.
Start your free trial with BuildPartner today to get the most accurate estimate of your construction project.
Frequently Asked Questions About The Cost To Build A Garage
Here are answers to common questions about the cost of building a garage.
What additional costs should I budget for when building a garage?
When building a garage, consider the costs of adding an electric vehicle (EV) charger, which typically ranges from £800–£1,500. Upgrading or paving the driveway to provide smooth access can cost anywhere between £1,000–£5,000, depending on the materials used. Additionally, if you need to adjust access to a public road, installing a dropped kerb can cost £1,000–£2,500.
Do I need planning permission to build a garage in the UK?
In the UK, garages under 30 square metres often fall under permitted development and require no planning permission if they meet specific criteria (e.g., height limits, no sleeping accommodation).
Boundary rules (e.g., Party Wall Act) may apply if the garage is built close to property lines. Additionally, restrictions for conservation areas or listed properties may require further permissions. Always check with your local planning authority for specific requirements.
For more information, see our related article which covers planning permission.
Will building a garage affect council tax band?
While adding a garage doesn’t automatically increase your council tax, your local council or the VOA (Valuation Office Agency in England and Wales, or the Scottish Assessors in Scotland) might reassess your property after the addition—although this is extremely rare.
What is the average daily rate for builders in the UK?
Builders typically charge £150 to £300 per day, while specialist trades (electricians, plumbers) may charge £200 to £400 per day. Check out our latest article on our blog for more information about the rates of different trades by region.
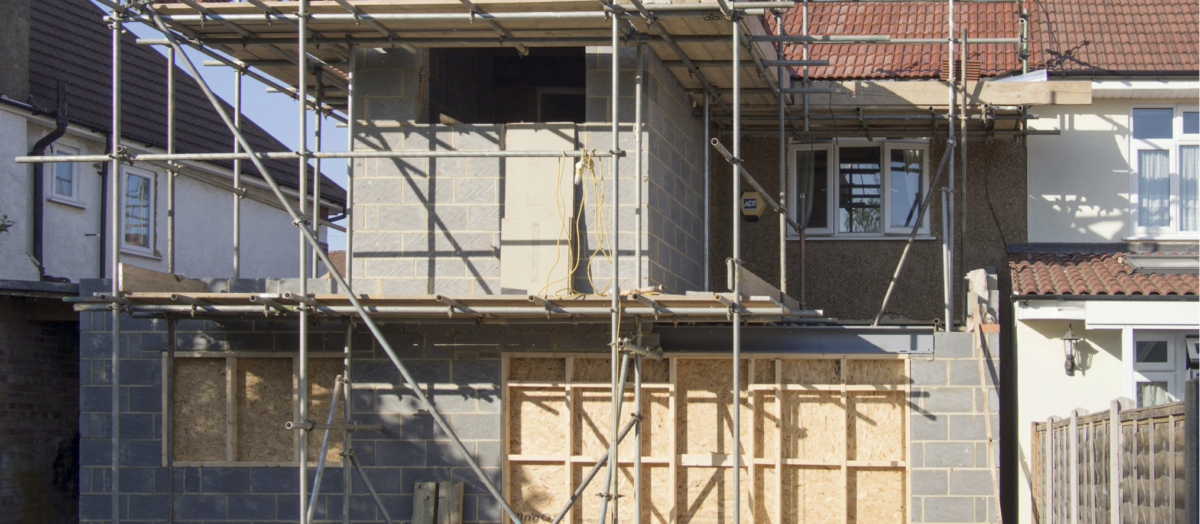
January 30th, 2025
Building an extension is an excellent way to increase living space and add value to your home, particularly when the alternative—moving house—is so expensive. However, costs vary significantly depending on factors such as the type of extension, location, materials used, and the complexity of the project.
In this guide, we break down the average costs of building a ground-floor and double-storey extension to help you understand what to expect when planning your construction project. We provide the average costs by region and also a breakdown of breakdown by project stage and room type.
Building An Extension In The UK
In our calculations, the costs of building an extension are based on the following:
- The roof of the extension is pitched, not flat.
- The extension is constructed out of brick/block, not a timber frame.
Also, the rooms in the calculation for the extension comprise:
- 20m² single-storey rear extension: dining room, utility room, WC.
- 40m² double-storey rear extension: dining room, utility room, WC, two bedrooms, an en-suite bathroom, storage room, small landing.
Start your free trial of BuildPartner today.
Which rooms you choose ultimately affects the overall cost of the extension. For instance, if we were adding a kitchen instead of a dining room, we would need to factor in the cost of fitting a kitchen and the appliances.
Calculations reflect the cost of fitting out the new rooms only. They do not include the remodelling of existing rooms or changes to the layout.
In terms of build specification, our pricing calculator has three options:
- Low spec is a basic finish; e.g. Leyland, Everest, Wickes.
- Mid spec is a standard finish; e.g. Dulux, Hamilton, Slim Line.
- High spec is a high-spec finish; e.g. Farrow & Ball, Fine Line, Siemens.
For the purposes of these extensions, we reviewed the costs for standard specification. Then, for each specification, we’ve provided a range of prices to reflect the varying types of contractors:
- Low benchmark – smaller companies are generally lower cost but less specialised and with low project management function; good for low/mid-spec projects and tight budgets.
- Mid benchmark – medium-sized companies offer a balanced mix of cost-effectiveness and specialisation; good for mid-range projects for effective execution within moderate budgets.
- High benchmark – larger companies generally have a higher cost base but can handle a wide variety of specialist tasks; good for mid/high-spec projects and project management.
Cost of Building A Ground-Floor Extension – Standard Spec
Here’s a table showing the average costs of building a single-storey rear extension for a standard-spec project in the UK:
Single-Storey Rear Extension | Total Average Build Cost | Average Cost Per Sq Metre | ||||
Low Benchmark | Mid Benchmark | High Benchmark | Low Benchmark | Mid Benchmark | High Benchmark | |
East Anglia | £79,067 | £86,255 | £93,443 | £2,636 | £2,875 | £3,115 |
London | £83,258 | £93,492 | £103,834 | £2,775 | £3,116 | £3,461 |
Midlands | £76,740 | £83,716 | £90,693 | £2,558 | £2,791 | £3,023 |
North England | £74,934 | £81,746 | £88,558 | £2,498 | £2,725 | £2,952 |
Northern Ireland | £77,293 | £84,275 | £91,298 | £2,575 | £2,809 | £3,043 |
Scotland | £77,334 | £84,364 | £91,395 | £2,578 | £2,812 | £3,046 |
South East | £83,142 | £92,968 | £102,038 | £2,771 | £3,099 | £3,401 |
South West | £77,518 | £89,564 | £98,302 | £2,670 | £2,985 | £3,277 |
Wales | £74,938 | £83,795 | £89,986 | £2,498 | £2,793 | £3,000 |
Average | £78,247 | £86,686 | £94,394 | £2,618 | £2,890 | £3,146 |
All costs exclude VAT.
Here’s what the data shows for the cost of building a single-storey rear extension to a standard spec:
- It costs 9% more to build an extension in London than in other regions.
- The minimum cost is £74,934, and the maximum cost is £103,834.
- The total average cost is £86,443, or £2,885 per square metre.
Housebuilding Cost Breakdown By Project Stage – London
Here’s an example of the associated costs for the different stages of building an extension for a standard-spec project – when using a mid-benchmark contractor in London:
Total | £93,492 | 100.0% |
External wall structure and lining | £14,024 | 15.0% |
Foundations and substructure | £13,159 | 14.1% |
Roof structure and coverings | £11,540 | 12.3% |
Steel and structural supports | £8,133 | 8.7% |
Floor preparation and finishes | £5,966 | 6.4% |
Units, worktops and kitchen appliances | £4,457 | 4.8% |
Heating and cooling | £4,198 | 4.5% |
External windows and doors | £3,984 | 4.3% |
Decoration | £3,927 | 4.2% |
Preliminaries | £3,564 | 3.8% |
Floor structure and lining | £3,555 | 3.8% |
Wired appliances | £3,239 | 3.5% |
Internal wall structure and lining | £2,711 | 2.9% |
Drainage and pipework | £2,427 | 2.6% |
Wall preparation and finishes | £2,163 | 2.3% |
Internal doors and frames | £1,517 | 1.6% |
Plumbed appliances | £1,373 | 1.5% |
Demolitions | £1,346 | 1.4% |
Wiring and fuseboards | £634 | 0.7% |
Ceiling structure and lining | £581 | 0.6% |
Ceiling preparation and finishes | £567 | 0.6% |
Fixtures and fittings | £426 | 0.5% |
Cost Breakdown By Room – London
Here’s a breakdown of the associated costs by room for building a standard-spec extension – when using a mid-benchmark contractor in London:
Total | £93,492 | 100% |
Ground Floor Rear Extension with pitched roof | £60,362 | 64.6% |
Utility | £13,821 | 14.8% |
Dining room | £10,902 | 11.7% |
WC | £7,912 | 8.5% |
P | Preliminaries | £496 | 0.5% |
Cost of Building A Double-Storey Extension – Standard Spec
Here’s a table showing the average costs of building a double-storey extension for a standard-spec project in the UK:
Double-Storey Rear Extension (Pitched Roof) | Total Average Build Cost | Average Cost Per Sq Metre | ||||
Low Benchmark | Mid Benchmark | High Benchmark | Low Benchmark | Mid Benchmark | High Benchmark | |
East Anglia | £131,357 | £143,298 | £155,240 | £2,189 | £2,388 | £2,587 |
London | £138,434 | £155,344 | £173,574 | £2,307 | £2,589 | £2,893 |
Midlands | £127,393 | £138,974 | £150,555 | £2,123 | £2,316 | £2,509 |
North England | £124,191 | £135,481 | £146,771 | £2,070 | £2,258 | £2,446 |
Northern Ireland | £128,347 | £139,658 | £151,296 | £2,134 | £2,328 | £2,522 |
Scotland | £128,673 | £140,371 | £152,069 | £2,145 | £2,340 | £2,534 |
South East | £138,130 | £154,455 | £169,524 | £2,302 | £2,574 | £2,825 |
South West | £128,668 | £148,454 | £162,937 | £2,213 | £2,474 | £2,716 |
Wales | £124,572 | £139,295 | £149,616 | £2,076 | £2,322 | £2,494 |
Average | £129,974 | £143,926 | £156,842 | £2,173 | £2,399 | £2,614 |
All costs exclude VAT.
Here’s what the data shows for the cost of building a double-storey extension to a standard spec:
- The minimum cost is £124,191, and the maximum cost is £173,574.
- The total average cost is £143,581, or £2,395 per square metre.
Average Cost To Build An Extension In 2025
So, how much does it cost to build an extension in the UK? Based on building to a standard specification, you can expect building an extension to cost on average (when using a mid-benchmark contractor):
- Ground-floor rear extension– £86,686, or £2,890 per square metre.
- Double-storey rear extension– £143,926, or £2,399 per square metre.
Please remember that these costs do not include VAT, and there may be other additional costs, such as obtaining planning permission, conducting structural surveys, making unexpected repairs, and completing custom finishes.
Start your free trial with BuildPartner today to get the most accurate estimate of building an extension based on your own dimensions and specifications.
FAQs About Building An Extension In The UK
Here are some frequently asked questions about building extensions in the UK.
What are the different types of extensions?
Common ground-floor extensions include rear, side, double-storey, and wraparound. A rear extension expands the back, while a side extension adds space to the side of the property. A double-storey extension increases space both upstairs and downstairs, and a wraparound extension combines rear and side extensions for a larger, open-plan space.
Do I need planning permission for an extension?
There are many variables to assess to determine if planning permission is needed when building an extension. For example, you need planning permission if your single-storey rear extension is higher than four metres or extends beyond the rear of the “original house” by more than six metres.
In many cases, extensions fall under permitted development rights. Find out more about planning permission in our guide here.
Do I need a Party Wall Agreement?
If your extension affects a shared wall or boundary with a neighbour, the Party Wall Act 1996 requires you to serve notice and potentially obtain their consent.
How Much Does It Cost To Build A House In 2025? A UK Guide
- Post author By ken
- Post date March 20, 2025
- No Comments on How Much Does It Cost To Build A House In 2025? A UK Guide
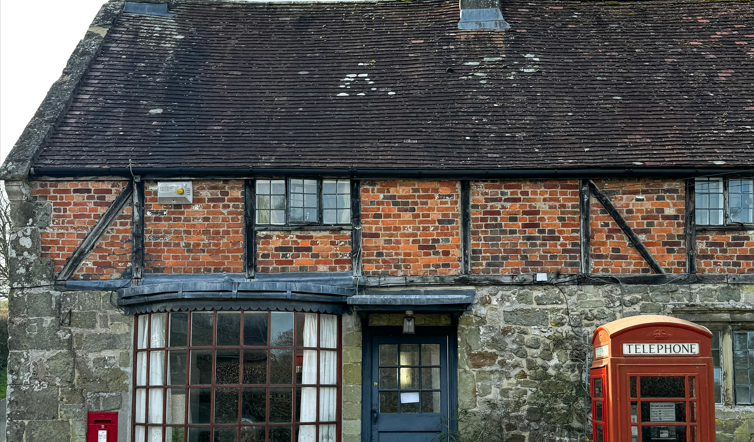
January 30th, 2025
As the UK grapples with a cost-of-living crisis and a volatile housing market, building a home in 2025 presents significant challenges. Construction costs per square metre are at historic highs, driven by inflation, material shortages, and changing regulations.
This guide not only explores average costs by region—including East Anglia, London, the Midlands, and more—but also provides a breakdown of expenses by project stage and room type, offering a detailed understanding of where your budget is likely to go.
Building A House In The UK
House-building costs vary significantly depending on many factors. Sources like Checkatrade offer a general estimate of £1,750 to £2,750 per square metre, while Purple Bricks suggests a lower average of £1,200 to £1,500 per square metre. However, these figures lack context regarding specification or regional variations, offering only a basic rule of thumb.
So, in our calculations, we applied a consistent methodology across different regions, focusing on a three-bedroom detached house. The average number of bedrooms in the UK is 2.95, so we rounded it up to 3 in our estimations. The floorplan was based on the average total floor area of a dwelling in the UK, which is 94m2.
Rooms included in this build are three bedrooms, a bathroom, a kitchen, a living room, a dining room, a cloakroom, the hallway and landing, and a dedicated boiler and storage cupboard.
A garage was excluded from our calculations since only a third of UK homes have one.
In terms of build specification, our pricing calculator has three options:
- Low spec is a basic finish; e.g. Leyland, Everest, Wickes.
- Mid spec is a standard finish; e.g. Dulux, Hamilton, Slim Line.
- High spec is a high-spec finish; e.g. Farrow & Ball, Fine Line, Siemens.
For the purposes of this comparison of build costs per square metre, we have reviewed the costs for all three specifications.
In addition, for each specification, we’ve provided a range of prices to reflect the varying types of contractors:
- Low benchmark – smaller companies are generally lower cost but less specialised and with low project management function; good for low/mid-spec projects and tight budgets.
- Mid benchmark – medium-sized companies offer a balanced mix of cost-effectiveness and specialisation; good for mid-range projects for effective execution within moderate budgets.
- High benchmark – larger companies generally have a higher cost base but can handle a wide variety of specialist tasks; good for mid/high-spec projects and project management.
Cost of Building A 3-Bedroom UK House – Basic Spec
Here’s a table showing the average costs of building a 3-bed house for a basic-spec project in the UK:
3-Bedroom Detached House (Basic) |
Total Average Build Cost |
Average Cost Per Sq Metre |
||||
Low Benchmark |
Mid Benchmark |
High Benchmark |
Low Benchmark |
Mid Benchmark |
High Benchmark |
|
East Anglia |
£259,469 |
£283,057 |
£306,645 |
£2,760 |
£3,011 |
£3,262 |
London |
£275,482 |
£308,910 |
£342,655 |
£2,931 |
£3,286 |
£3,645 |
Midlands |
£251,343 |
£274,193 |
£297,042 |
£2,674 |
£2,917 |
£3,160 |
North England |
£244,562 |
£266,794 |
£289,027 |
£2,602 |
£2,838 |
£3,075 |
Northern Ireland |
£253,082 |
£275,473 |
£298,429 |
£2,686 |
£2,931 |
£3,175 |
Scotland |
£253,646 |
£276,705 |
£299,764 |
£2,698 |
£2,944 |
£3,189 |
South East |
£274,096 |
£306,489 |
£336,390 |
£2,916 |
£3,261 |
£3,579 |
South West |
£253,757 |
£293,829 |
£322,495 |
£2,795 |
£3,126 |
£3,431 |
Wales |
£244,740 |
£273,664 |
£294,366 |
£2,604 |
£2,911 |
£3,132 |
Average |
£256,686 |
£284,346 |
£309,646 |
£2,741 |
£3,025 |
£3,294 |
All costs exclude VAT.
Here’s what the data shows for the cost of building a 3-bed house to a basic spec:
- It costs 10% more to build a 3-bed house in London than in other regions.
- The minimum cost is £244,562, and the maximum cost is £342,655.
- The total average cost is £283,559, or £3,020 per square metre.
Housebuilding Cost Breakdown By Project Stage – London
Here’s an example of the associated costs for the different stages of building a house for a basic-spec project – when using a mid-benchmark contractor in London:
Total |
£308,910 |
100.0% |
External wall structure and lining |
£60,267 |
19.5% |
Foundations and substructure |
£35,960 |
11.6% |
Roof structure and coverings |
£35,449 |
11.5% |
Preliminaries |
£21,126 |
6.8% |
Floor structure and lining |
£20,470 |
6.6% |
External windows and doors |
£16,160 |
5.2% |
Steel and structural supports |
£13,625 |
4.4% |
Internal wall structure and lining |
£12,730 |
4.1% |
Decoration |
£11,536 |
3.7% |
Floor preparation and finishes |
£11,042 |
3.6% |
Heating and cooling |
£10,860 |
3.5% |
Units, worktops and kitchen appliances |
£10,650 |
3.4% |
Wall preparation and finishes |
£9,044 |
2.9% |
Wired appliances |
£8,787 |
2.8% |
Drainage and pipework |
£8,357 |
2.7% |
Plumbed appliances |
£5,226 |
1.7% |
Ceiling structure and lining |
£3,875 |
1.3% |
Internal doors and frames |
£3,650 |
1.2% |
Stairs, balustrades and lifts |
£2,910 |
0.9% |
Wiring and fuseboards |
£2,764 |
0.9% |
Ceiling preparation and finishes |
£1,726 |
0.6% |
Demolitions |
£1,385 |
0.4% |
Fixtures and fittings |
£ 763 |
0.2% |
Joinery |
£ 546 |
0.2% |
Cost Breakdown By Room – London
Here’s a breakdown of the associated costs by room for a basic-spec house build – when using a mid-benchmark contractor in London:
Total |
£308,910 |
100% |
G | Ground Floor |
£115,953 |
37.5% |
I | First Floor |
£62,359 |
20.2% |
R | Pitched roof |
£35,449 |
11.5% |
Kitchen |
£29,752 |
9.6% |
Bathroom |
£10,592 |
3.4% |
En-suite |
£9,087 |
2.9% |
Living room / family room |
£7,266 |
2.4% |
Bedroom 1 |
£6,973 |
2.3% |
WC |
£6,404 |
2.1% |
Bedroom 2 |
£6,096 |
2.0% |
Bedroom 3 |
£6,096 |
2.0% |
Boot Room / Cloakroom |
£5,436 |
1.8% |
Landing incl. stairs |
£4,265 |
1.4% |
Boiler Cupboard |
£3,182 |
1.0% |
Cost of Building A 3-Bedroom UK House – Standard Spec
Here’s a table showing the average costs of building a 3-bed house for a standard-spec project in the UK:
3-Bedroom Detached House (Standard) |
Total Average Build Cost |
Average Cost Per Sq Metre |
||||
Low Benchmark |
Mid Benchmark |
High Benchmark |
Low Benchmark |
Mid Benchmark |
High Benchmark |
|
East Anglia |
£279,511 |
£304,922 |
£330,332 |
£2,974 |
£3,244 |
£3,514 |
London |
£295,524 |
£331,321 |
£367,252 |
£3,144 |
£3,525 |
£3,907 |
Midlands |
£271,386 |
£296,057 |
£320,729 |
£2,887 |
£3,150 |
£3,412 |
North England |
£264,604 |
£288,659 |
£297,852 |
£2,815 |
£3,071 |
£3,169 |
Northern Ireland |
£273,124 |
£297,338 |
£322,115 |
£2,900 |
£3,163 |
£3,427 |
Scotland |
£273,689 |
£298,570 |
£323,451 |
£2,912 |
£3,176 |
£3,441 |
South East |
£294,138 |
£328,900 |
£360,987 |
£3,129 |
£3,499 |
£3,840 |
South West |
£273,800 |
£316,240 |
£347,093 |
£3,009 |
£3,364 |
£3,692 |
Wales |
£264,783 |
£296,075 |
£318,053 |
£2,817 |
£3,150 |
£3,384 |
Average |
£276,729 |
£306,454 |
£331,985 |
£2,954 |
£3,260 |
£3,532 |
All costs exclude VAT.
Here’s what the data shows for the cost of building a 3-bed house to a standard spec:
- The minimum cost is £264,604, and the maximum cost is £367,252.
- The total average cost is £305,056, or £3,249 per square metre.
Cost of Building A 3-Bedroom UK House – Premium Spec
Here’s a table showing the average costs of building a 3-bed house for a premium-spec project in the UK:
3-Bedroom Detached House (Premium) |
Total Average Build Cost |
Average Cost Per Sq Metre |
||||
Low Benchmark |
Mid Benchmark |
High Benchmark |
Low Benchmark |
Mid Benchmark |
High Benchmark |
|
East Anglia |
£314,534 |
£343,128 |
£371,722 |
£3,346 |
£3,650 |
£3,954 |
London |
£330,547 |
£370,483 |
£410,235 |
£3,516 |
£3,941 |
£4,364 |
Midlands |
£306,409 |
£334,264 |
£362,120 |
£3,260 |
£3,556 |
£3,852 |
North England |
£299,627 |
£326,866 |
£354,105 |
£3,188 |
£3,477 |
£3,767 |
Northern Ireland |
£308,147 |
£335,544 |
£363,506 |
£3,278 |
£3,570 |
£3,867 |
Scotland |
£308,712 |
£336,777 |
£364,841 |
£3,284 |
£3,583 |
£3,881 |
South East |
£329,161 |
£368,062 |
£403,970 |
£3,502 |
£3,916 |
£4,298 |
South West |
£308,823 |
£355,402 |
£390,076 |
£3,285 |
£3,781 |
£4,150 |
Wales |
£299,806 |
£335,237 |
£359,444 |
£3,189 |
£3,566 |
£3,824 |
Average |
£311,752 |
£345,085 |
£375,558 |
£3,317 |
£3,671 |
£3,995 |
All costs exclude VAT.
Here’s what the data shows for the cost of building a 3-bed house to a premium spec:
- The minimum cost is £299,627, and the maximum cost is £410,235.
- The total average cost is £344,131, or £3,661 per square metre.
Average Cost To Build A House In 2025
So, how much does it cost to build a new house in the UK? Based on the three different specifications covered in this article, you can expect building a 3-bedroom house to cost on average (when using a mid-benchmark contractor):
- 3-bedroom house: basic spec – £284,346, or £3,025 per square metre.
- 3-bedroom house: standard spec – £306,454, or £3,260 per square metre.
- 3-bedroom house: premium spec – £345,085, or £3,671 per square metre.
Please remember that these costs do not include VAT, and there may be other additional costs, such as obtaining planning permission, conducting structural surveys, making unexpected repairs, and completing custom finishes.
Start your free trial with BuildPartner today to get the most accurate estimate of building a house based on your own dimensions and specifications.
FAQs About Housebuilding Costs In The UK
Here are some frequently asked questions about housebuilding costs in the UK.
Will I pay VAT on self-build projects in the UK?
New-build homes are generally zero-rated for VAT. This means that while contractors and suppliers of building materials may charge VAT on their services, you can reclaim it.
You can reclaim VAT on integral fixtures like kitchens, bathrooms, and heating systems. However, VAT cannot be claimed on professional services, landscaping, driveways, or non-integral items like luxury fittings (e.g., Jacuzzis).
Will Labour’s pledge to build 1.5 million homes affect building costs?
Labour’s pledge to build 1.5 million homes by 2029 could have mixed effects on building costs. While an increase in housing supply may help alleviate pressure on the housing market in the long run, it could also lead to a surge in demand for construction materials and skilled trades, pushing up material costs and labour prices, particularly in areas where construction activity is already high.